「專家視野」鑄造生產過程在線快速檢測技術研究及應用進展
摘要
隨著智能鑄造、綠色鑄造步伐的不斷加快,鑄造生產過程檢測技術特別是在線檢測技術的重要性愈加突出。為了進一步提高我國鑄造檢測技術研究及應用水平,服務智能鑄造車間構建,本文綜述了合金熔體質量、型砂及砂型質量、鑄件質量三大方面的檢測與監測技術的研究及應用進展概況,簡要分析了主要在線檢測技術的發展趨勢。
我國鑄件年產量連續多年穩居世界首位,從生產規模和產量看,早已是名副其實的鑄造大國。但在生產效率和產品質量等方面,與發達國家差距依然較大。在全球鑄造生產追求智能化、綠色化目標的背景下,中國鑄造產業尋優快進,變鑄造大國為鑄造強國,是廣大鑄造工作者多年的夢想。
鑄造是將固態原料變成液態熔體再變成固態鑄件的過程,或者說是一種利用固-液和液-固兩個轉變獲取所需零部件(或其毛坯)的生產工藝。如果說合格的金屬或合金熔體、合格的鑄型及合理的澆注工藝,是獲得合格鑄件的必要條件,對熔煉過程、配砂及造型過程以及鑄件質量實施在線檢測則是實現必要條件的必要條件。
歷經多年發展,我國鑄造檢測技術已有長足進步,從簡單參數手動檢測到復雜參數自動檢測,從單一參數模擬記錄到多參數智能分析,與國外先進鑄造檢測技術的差距日漸縮小。當前的智能鑄造車間建設給鑄造檢測技術提出了更高的要求,作為智能鑄造重要組成部分的智能感知單元,鑄造在線檢測需要完成更多角度、更快速度和更高精度的參數檢測。鑄造檢測技術面臨嚴峻挑戰的同時,也迎來了難得的發展機遇。
本文分鑄造合金熔體質量檢測、型砂及砂型質量檢測、鑄件質量無損檢測三大方面,回顧在線檢測技術研究及應用進展并分析其發展趨勢,旨在找出短板、發現空間、挖掘潛力,促進在線檢測技術快速發展。受筆者領域視野及學術認知所限,綜述不全面、評述不準確在所難免,懇請同行批評指正。
1 鑄造合金熔體質量檢測技術
評價鑄造合金熔煉質量的標準是熔體質量,實際生產中最受關注的熔體質量指標是熔體溫度、化學成分、純凈度及結晶后組織性能。
1.1 熔體溫度檢測
熔體溫度控制對合金熔煉、爐前處理及澆注過程優化控制均具有重要影響,熔體溫度精準控制與鑄造工藝有機結合也是獲得優質鑄件的重要途徑。
隨著遠紅外測溫等技術的不斷進步,非接觸測溫已經成為許多鑄造企業合金熔體爐前測溫的重要或主要手段。為了兼顧檢測精度和檢測成本,也有準接觸測溫技術的研究,采用一種低成本管體探頭浸入被測熔體,熔體熱輻射經管腔射向紅外敏感器件,經變換后輸出熔體溫度。當前和今后一個時期,熔體測溫技術需要解決的兩個問題是,最大限度消除遠紅外等非接觸測溫的影響因素,進一步提高其測溫精度;以半永久型偶頭替代快換偶頭,進一步降低熱電偶測溫的檢測成本。
除關注測溫技術本身技術進步外,日本鑄造企業的熔體溫度管理模式值得借鑒。熔體溫度管理的三個要點是:①熔煉時,在熔體溫度上升過程中無線檢測熔體溫度,系統顯示出當前溫度并預測升至預設最高爐溫所需時間,儀表循環測溫并顯示溫度和時間,達到設定溫度時發出聲光警報;②熔體出爐轉入澆包后,由無線溫度檢測儀循環檢測澆包內熔體溫度,實時顯示當前溫度值和降至設定溫度所需時間,達到設定溫度時發出聲光警報;③熔體澆注時,無線檢測儀實時檢測熔體溫度,當溫度降至設定澆注溫度范圍內時發出光警報,而達到澆注溫度時則發出聲光警報。溫度精準管控帶來鑄件品質提升及性能穩定的結果不言而喻。
1.2 合金熔體化學成分快速檢測
實際生產中,往往因原材料成分檢驗、配料加料以及熔煉控制等環節出現問題而導致熔體化學成分偏離設計范圍。因此,熔體化學成分是許多鑄造企業必有的爐前檢驗內容。
受檢測速度的限制,早期的熔體化學成分檢驗多在爐后完成,滯后的檢驗報告無法用于熔體質量閉環控制。雖然熱分析方法可以用于鑄鐵含碳、含硅及碳硅當量的快速分析及個別鋁合金主要成分分析,但分析元素數量十分有限且影響因素較多,難以成為合金熔體化學成分快速分析的主要手段。
近年來,為了滿足鑄造合金熔體化學成分爐前快速檢測的需要,一方面針對傳統化學分析法的技術進步在加快,種類繁多的化學成分分析儀不斷推出;另一方面,隨著國內外光譜技術的快速發展,一定規模的鑄造工廠都先后配備了形式各異的化學成分直讀光譜儀,如日本日立系列臺式直讀光譜儀、德國產手持式直讀光譜儀、英國牛津儀器推出的手持式激光誘導擊穿光譜儀等。與此同時,國內研究機構也研究開發了國產自主品牌直讀光譜儀,產品性能受到用戶好評。
激光誘導擊穿光譜(Laser induced breakdownspectroscopy,簡稱 LIBS)技術的出現,為合金熔體成分原位檢測提供了更為快捷的手段。LIBS將激光聚焦到樣品表面產生等離子體,用光譜儀和探測器對等離子體輻射光譜信號進行采集分析,進而推導出樣品中元素種類和含量,具有無需制樣、微損、快速、遠程實時在線檢測和多元素同時分析等優點。
國外報導LIBS技術已成功用于鋼熔體中可熔性元素如C、Cr、Cu、Mn和Ni元素以及鋁合金熔體中Si、Mg、Fe、Mn和其他合金化元素的在線測控。
LIBS 技術在國內冶金行業的應用已經開始,鑄造車間爐前采用LIBS快速檢測熔體化學成分尚處起步階段。林京君搭建了基于LIBS技術的在線檢測平臺,實現了對鋼鐵元素的高精度分類識別、定量分析、回收熔融再利用。羅丹利用LIBS技術對中低合金鋼和TC11鈦合金進行了定量分析,并與Spark-OES和ICPOES測定結果對比分析,表明LIBS分析速度優勢明顯。
可以預見,LIBS技術不久將廣泛用于鑄造熔體化學分析。
1.3 合金熔體純凈度快速檢測
合金熔體凈化處理對提高或保證鑄件質量非常重要,對鋁合金而言,因其熔煉過程極易吸氣和氧化,以除氫和去氧化夾雜為主要目標的凈化處理已成為獲得合格鑄件的基本措施之一。為了快速準確評價合金熔體凈化處理前后的純凈度,國內外鑄造工作者多年來研究開發了多種測氫、測雜方法及裝置,并在生產中獲得了不同程度的應用。
1.3.1 鋁合金熔體含氫量檢測
鋁合金熔體與大氣中的水蒸氣及原輔材料(金屬爐料、變質劑、精煉劑等)中的水發生化學反應形成氫氣分子,在高溫下氫分子與鋁合金熔體表面發生碰撞被電離為氫原子,隨著氫原子數量的增加,氫原子由表面向熔體內部擴散,最后留存在鋁合金熔體中。
研究證明,氫在液、固態鋁合金中的溶解度相差近20倍,如果熔體凝固過程中氫氣不能及時排出,將會在鑄件內形成氣孔等缺陷。因此,鋁合金熔體澆注前必須進行充分除氫處理。
用于除氫處理前后熔體含氫狀態檢測的方法裝置有很多,多數基于Sievert定律實現含氫量計算。Sievert定律如式(1)所示:

式中:CH為鋁熔體中氫含量(cm3/100g);T為鋁熔體溫度(K);PH2為鋁熔體中氫分壓(Pa);A和B為與合金成分有關的溶解度常數。測得熔體的溫度和熔體中氫分壓值,即可算出熔體內的含氫量。根據獲取熔體氫分壓的方法不同,本文將測氫方法分為第一氣泡法、惰氣循環法、負壓抽吸法、濃差電池法和非氫分壓檢測法。
(1)第一氣泡法。第一氣泡法是20世紀40年代末由Dardel提出的一種取樣測定熔體氫分壓定量計算含氫量的測氫方法。首先取少量的鋁熔體澆入保溫坩堝,將其放入透明的密閉真空室并開啟真空泵。隨著熔體溫度和室內壓力降低,熔體內外部壓力差為氫擴散提供動力,致使熔體內部的氫形成氣泡向外擴散。測定第一個氣泡逸出時的熔體溫度和室內壓力,根據Sievert定律即可算出鋁熔體的含氫量。
基于該方法的測氫裝置如瑞士FMA公司生產的COMPACTⅡ型單功能快速測氫儀和ALU SPEED型多功能快速測氫儀,國內華中科技大學研制的AH型鋁液快速定量測儀都有不同程度的實際應用。
第一氣泡法具有設備相對簡單、測試成本低、測氫速度快的優點,對于含氫量大于0.3mL/100gAl的熔體,一般可在3min內完成檢測,檢測精度可以達到±0.05mL/100gAl。該方法的不足是,檢測計算結果與被檢熔體重量、抽真空速度以及冷卻速度等因素有很大關系,同時受人為觀測主觀因素的影響,因此測試的重復性有限。針對人為觀察判斷第一氣泡易出偏差的問題,許四祥等采用計算機圖像識別法判斷第一氣泡的出現,文獻報道對提高第一氣泡法計算精度和檢測重復性方面有較大改善。
(2)惰氣循環法。惰性氣體循環法是在20世紀50年代中期由Ransley提出的一種熔體含氫量原位定量檢測方法,其工作原理如圖1所示。將惰性氣體(氬氣或氮氣)經特制探頭送入被測熔體并收回和在循環管路不斷循環,惰氣在熔體中停留過程中由于吸入熔體中的氫而使循環氣體的氫濃度逐漸升高,當循環氣體氫分壓與熔體氫分壓相等時,熔體氫不再向氣體中擴散。循環氣體氫濃度的變化及平衡狀態可通過串接在循環回路中的熱導池實時監測,平衡狀態下熱導池輸出信號轉化為氣體氫分壓,利用Sievert定律即可計算熔體的含氫量。
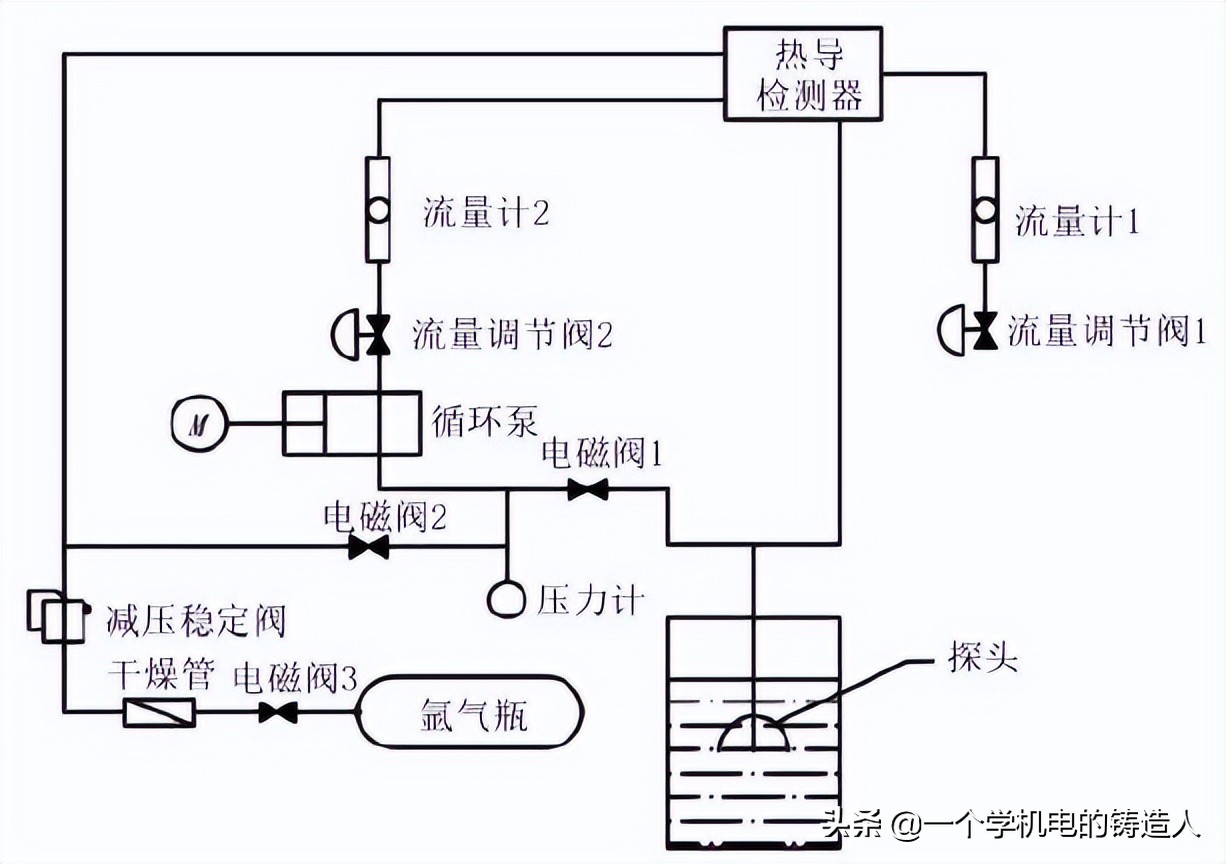
圖1 惰性氣體循環法測氫裝置示意圖
惰性氣體循環法是較早用于實際生產的鋁合金熔體原位快速測氫方法之一。基于惰氣循環測氫原理開發的測氫儀,所用探頭主要有開放式和閉合式兩類。
美國鋁業公司首次研制的Telegas測氫儀及國內西南鋁業開發的ELH測氫儀均采用開放式探頭,加拿大ABB公司開發的ALSCAN測氫儀等采用閉合式探頭。
惰氣循環法熔體原位測氫的優點是操作簡便,可靠性高,缺點是檢測速度仍顯緩慢,這也正是后續改進惰氣循環測氫儀的空間所在,縮短擴散平衡時間以提高測氫速度將是研究重點。
(3)負壓抽吸法。負壓抽吸法是一種將特制探頭浸入被測熔體,熔體氫通過探頭向真空室擴散,通過測定擴散平衡時真空室內壓力獲得熔體氫分壓,進而利用Sievert定律計算氫含量的熔體原位測氫方法。
生產中應用較多的負壓抽吸法測氫裝置是歐洲RWTH-Aachen鑄造技術研究所研究開發的哈培爾法(CHAPEL) 測氫儀,其工作原理和儀器實物照片如圖2所示。氣密陶瓷管一端與真空系統和壓力傳感器連接,另一端與多孔石墨探頭連接,將多孔石墨探頭直接浸入被測鋁液中。迅速抽去探頭內空氣,鋁液中的氫氣逐漸向石墨探頭中擴散,直至石墨探頭中氫分壓與鋁液中氫分壓達到動態平衡為止。為了解決檢測精度與檢測速度之間的矛盾,哈培爾測氫法采取了向真空室注氫促進擴散快速平衡的措施。
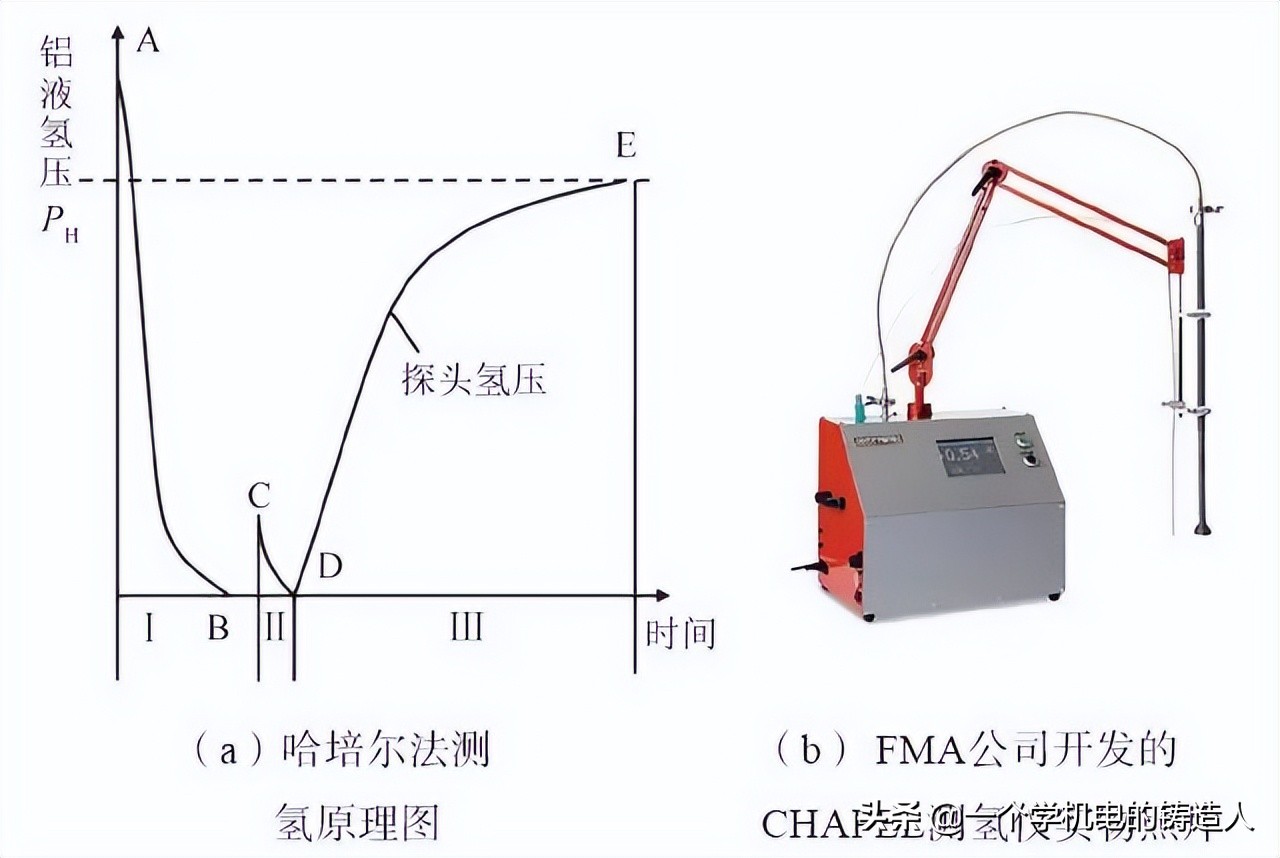
圖2 測氫原理圖及實物照片
華中科技大學熊艷才等采用石墨探頭浸入熔體直接抽真空檢測熔體含氫量,平衡時間與熔體含氫量相關,平均時間在5min左右。
哈爾濱理工大學鑄造測控技術研究室于2005年開始負壓抽吸測氫新方法研究,先后完成動態呼吸、負壓回升速率及變容真空室快速測氫方法研究。由于采用真空室容積動態變化和擴散平衡點動態求解等新技術,可使檢測周期大為縮短,不足1min即可完成測試。此外,研制的配套一次性探頭制造方便、成本低廉,更有助于新型測氫儀器推廣應用。
(4)濃差電池法。濃差電池法是1978年由R.Gee等人提出的一種新型在線連續測氫方法。其突出優點是測試速度快、檢測精度高,且可實現在線連續測氫,但其固體電解質穩定性差、易分解等問題還有待繼續研究解決。
實際生產中應用較早的濃差電池法測氫裝置,是日本名古屋工業大學和TYK公司合作開發的NOTORP型測氫儀,如圖3所示。由于測試時外部氫氣不斷地給傳感器提供氫分壓穩定的參比氣氛,省去了熔體氫的緩慢擴散過程,從而大大縮短了檢測時間。NOTORP型測氫儀的不足之處是所用導電質子陶瓷材料熱沖擊能力較差,極易損壞,同時設備成本較高。
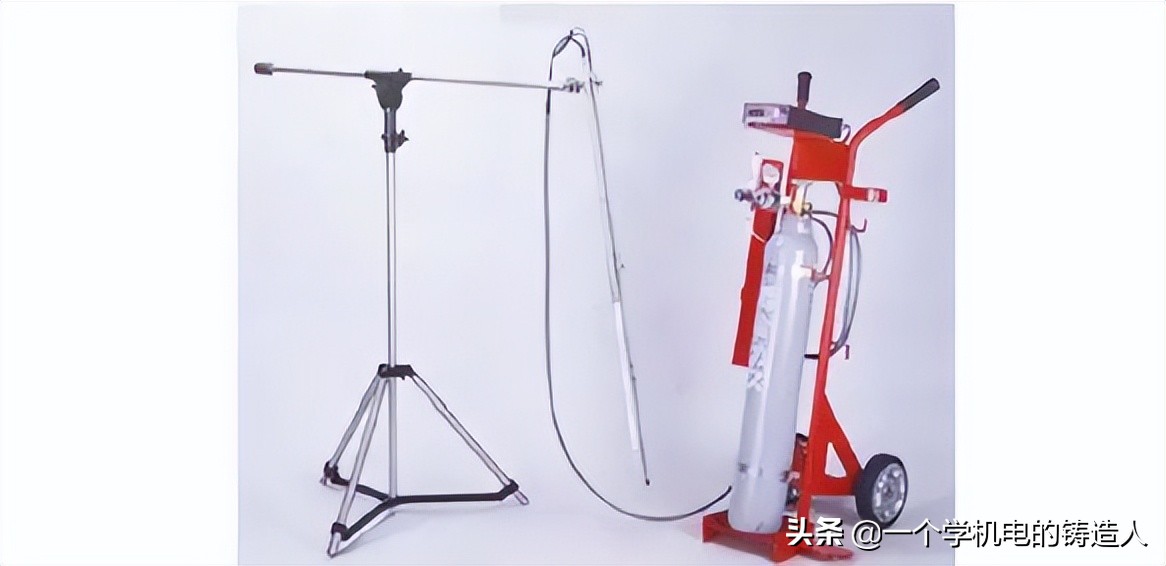
圖3 NOTORP型測氫儀
濃差電池法測氫儀因測試速度快的突出優點而深得用戶歡迎,開發固體電解質新材料、提高其熱穩定性和創新濃差電池新結構,是科技工作者關注并致力解決的關鍵問題。華中科技大學開發了由金屬氫化物提供氫分壓的氫濃差電池,結構簡圖如圖4所示。其中電解質管與鋁熔體不直接接觸,可避免探頭插入熔體時過大的熱沖擊。東北大學王常珍教授與日本名古屋大學巖原弘育教授合作,取得了我國濃差電池測氫技術的長足進展,所研制的氫傳感器經多廠現場測試,響應時間快至2~3s,靈敏度達到0.001mL/100gAl,測量范圍0.001~1.000mL/100gAl,檢測結果與Telegas法高度一致,具有極為廣闊的應用前景。
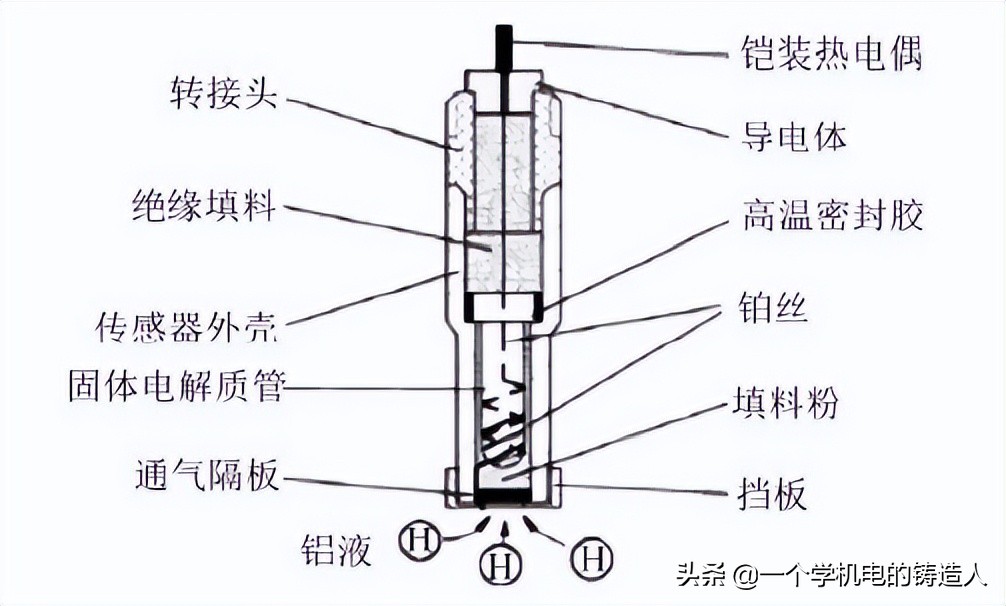
圖4 氫化物氫分壓濃差電池結構簡圖
(5)非氫分壓測氫法。無需借助熔體氫分壓實現含氫量測量的方法統稱為非氫分壓測氫法,主要有減壓凝固稱重法、凝固過程聲發射檢測法等。
減壓凝固稱重法應用歷史較長,有時也被用于標定其他測氫新方法的標準方法。如圖5所示,將被測熔體澆入特制樣杯后放入負壓凝固室,控制試樣在合適的壓力和溫度下凝固,使試樣中氫氣既能充分析出又不逸出試樣之外。
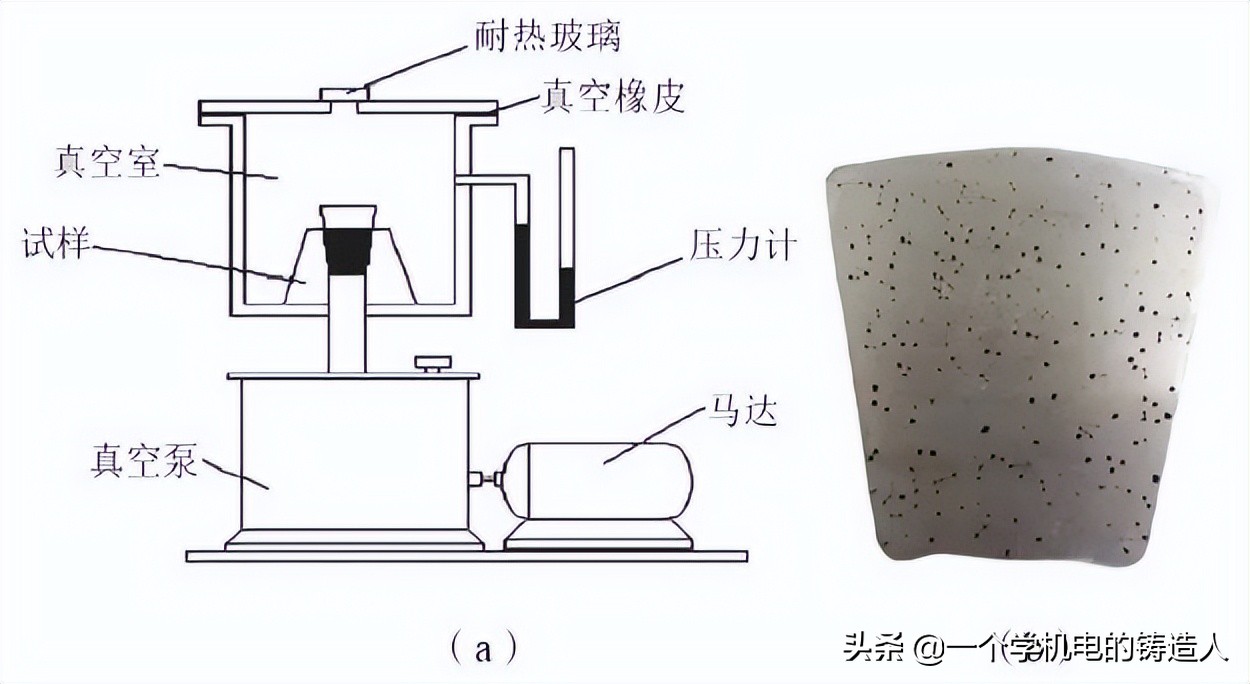
圖5 減壓凝固法試樣制備裝置結構簡圖及含氣試樣剖面照片
利用高精度天平分別測定試樣在空氣和水中的重量,算得含氣試樣密度并與被測合金標準密度比較,經簡單計算求得被測合金熔體含氣量。基于減壓凝固稱重原理的測氫裝置很多,但理想含氣試樣獲得并不簡單。近年來,有關減壓凝固試樣制備方法的研究成果,都從不同角度為后續研究提供了有益參考。解決減壓凝固工藝穩定性和試樣密度快捷精準測定問題,是進一步提高減壓凝固稱重測氫法實用性的關鍵。
凝固過程聲發射檢測法是2002年由俄羅斯Vorontsov V B等人提出的一種不需借助氫分壓的取樣測氫方法,測氫裝置結構簡圖如圖6所示。鋁合金熔體試樣在凝固時因氫溶解度大幅度下降而形成氣孔,氣孔周圍產生局部應力時將對外發射彈性波,通過壓電傳感器采集聲發射信號,可建立聲發射信號強度與熔體氫含量之間的關系。圖7是基于這一原理研制的Angara-2測氫儀實物照片。目前,雖然國內未見有同類儀器應用,但一種新穎測氫方法對研究開發新型測氫裝置具有參考價值。

圖6 凝固過程聲發射測氫裝置結構簡圖
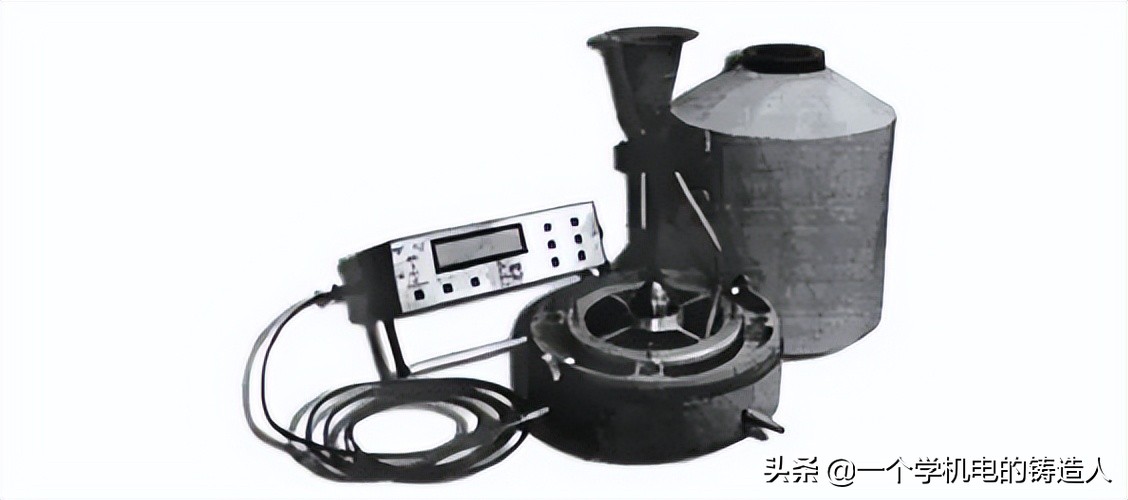
圖7 Angara-2 測氫儀實物照片
1.3.2 鋁合金熔體夾雜物含量檢測
鋁合金在熔煉過程中直接與爐氣接觸,其中的氮氣、氧氣和水蒸氣或以原子態溶解于合金熔體,或與合金熔體反應生成化合物進入合金熔體。各類夾雜物對鑄件性能均有重要影響,爐前測雜、除雜是鋁合金生產的重要環節。
熔體夾雜物檢測方法總體上可分為爐前快速金相法、過濾統計分析法和熔體原位在線檢測法三大類,第一類以試樣金相觀察為手段,一般用于定性和半定量分析,第二類以過濾熔體為手段,適合綜合評價,第三類以電流、超聲、射線為手段,具有檢測快捷的優勢。
(1)爐前快速金相法。最簡單的爐前快速金相法,是取少量熔體澆入試樣模具,快速凝固后切開試樣,磨平拋光后利用金相顯微鏡觀察夾雜物形態和分布情況,以此大致評價熔體夾雜含量。
另外一種金相觀察法是K形試樣法,取被測合金熔體澆入K形測雜取樣器,試樣凝固后在指定截面切開,通過金相觀察并統計不同斷面夾雜個數,代入式(2)計算K值,以此表征合金熔體夾雜含量。
K=S/n (2)
式中:K為斷面上夾雜數;S為n個試樣上總夾雜數;n為檢測的試樣數。有時K值也分K1、K3和K10,分別代表視野放大倍數為1倍、3倍和10倍下的K值。
(2)過濾統計分析法。基于熔體過濾原理的測雜方法,是鋁合金熔體在自身重力或外界壓力作用下流過過濾器(泡沫陶瓷),熔體中的夾雜富集在過濾片上,通過測定濾后熔體的重量和濾片面積占比等參數,可以得到鋁熔體夾雜含量。
PoDFA(Porous Disk Filtration Apparatus)法是由加拿大鋁業公司基于過濾統計分析法開發的一種測雜方法,裝置原理及實物外形如圖8所示。PoDFA法通過抽真空的方式使過濾片兩側形成壓力差,鋁熔體在負壓下通過由超細Al2O3粉燒結而成的過濾片落入下方容器并稱重,過濾結束后取出帶有夾雜物的過濾片并進行金相分析,以過濾片上夾雜物所占面積除以熔體的質量,得出單位質量熔體中夾雜物含量(單位為mm2/kg)。
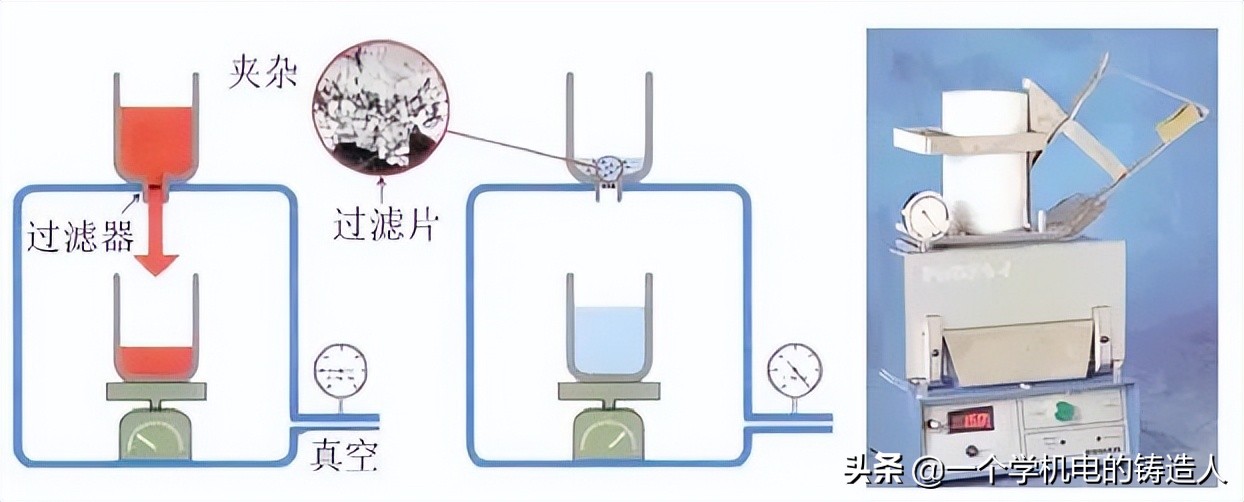
圖8 PoDFA法原理圖及裝置實物照片
Prefil-Footprinter法在PoDFA法的基礎上增加了過濾熔體質量與時間關系曲線,實現了熔體質量實時監測,其裝置示意圖如圖9所示。該方法是在等溫等壓的條件下,通過自動化系統監控鋁熔體流經過濾片,同時自動記錄過濾的熔體質量與時間的關系曲線。如圖10所示,過濾相同質量熔體所用時間越長,曲線斜率越小,說明夾雜物數量越多,熔體質量越差,反之則熔體的質量越好。Prefil-Footprinter法檢測速度快,適合在工業生產中實時監測鋁熔體中夾雜物含量,但由于其價格較高,并未在我國實際生產中獲得廣泛應用。
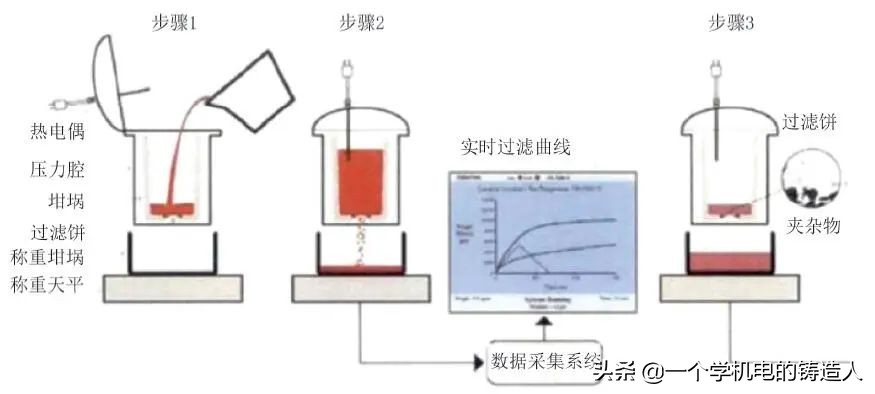
圖9 Prefil-Footprinter法工作原理圖
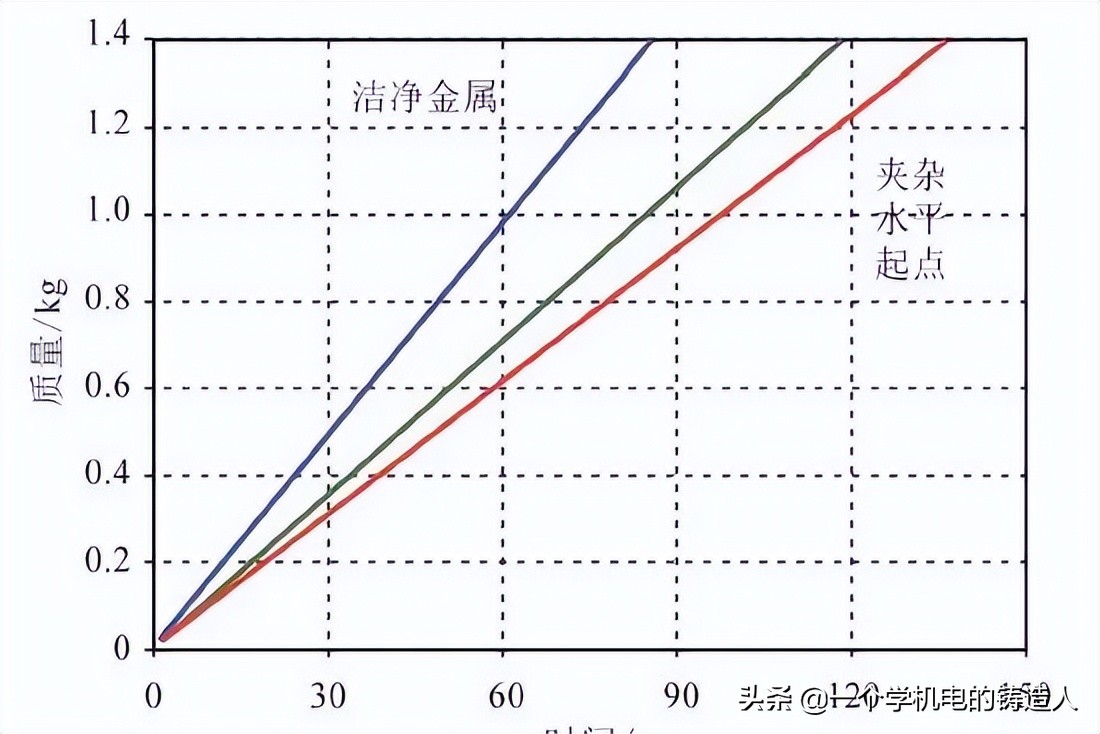
圖10 過濾熔體質量與時間關系曲線
(2)熔體原位在線檢測法。熔體夾雜的原位在線檢測通過電流、超聲或激光與固相顆粒的相互作用得以實現。典型在線檢測方法和裝置有LiMCA(LiquidMetal Cleanliness Analyzer)法、超聲探頭熔體夾雜在線檢測法和Reynolds 4-M SystemTM熔體監控器。
LiMCA(Liquid Metal Cleanliness Analyzer)法,是一種基于電敏感區原理檢測夾雜物含量的方法,最早由加拿大Bomen公司開發,其工作原理如圖11所示。
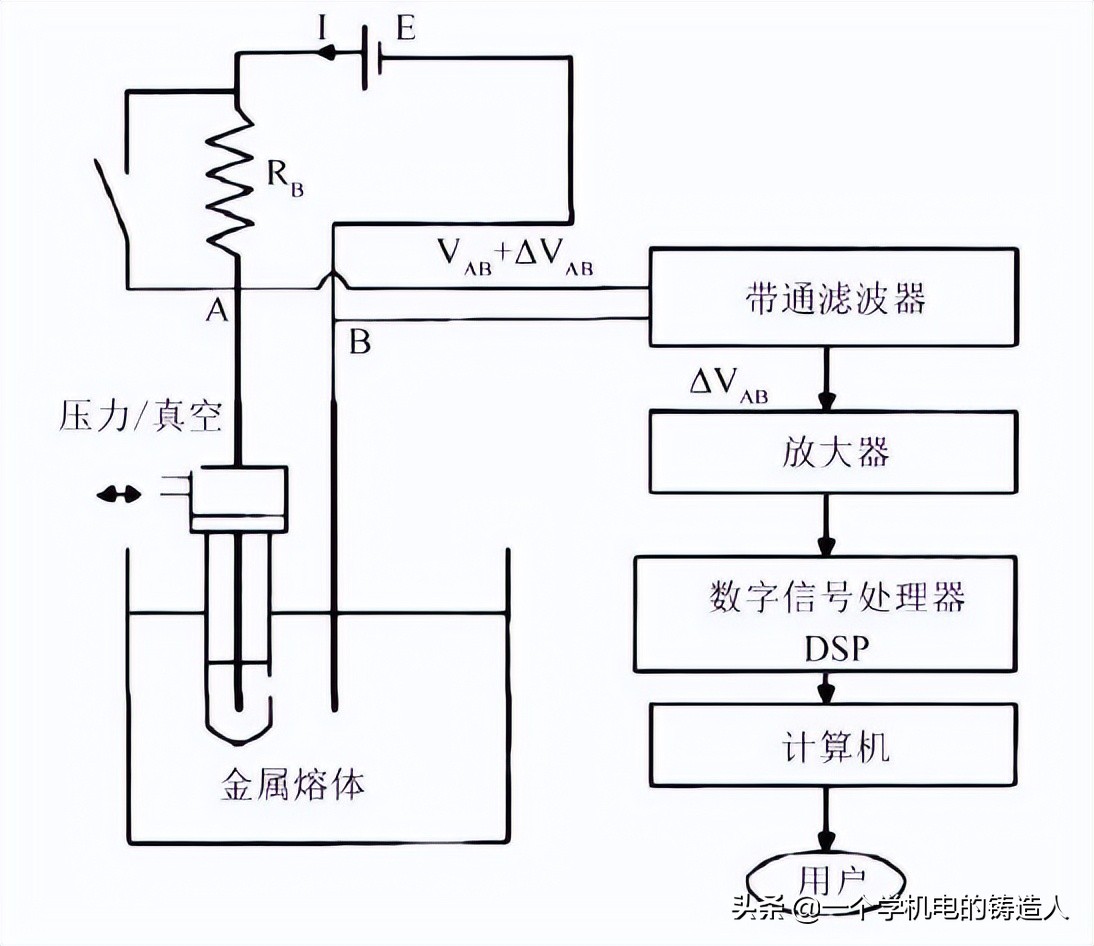
圖11 LiMCA法工作原理圖
將兩電極浸入被測熔體中,在兩電極之間通入恒定直流電,絕緣試管下端開有一個小孔,熔體在負壓作用下可經小孔進入試管,熔體中夾雜物通過小孔時會使電阻增加,利用回路產生的脈沖電壓可以檢測夾雜物數量。孔徑大小決定可測量夾雜物的尺寸,當小孔直徑為300μm時,能檢測到的夾雜物最小尺寸約為20μm。
LiMCA法檢測速度快,同時可根據需要檢測不同區域的夾雜分布。但也存在小孔易堵塞和遇導電性金屬間化合物夾雜導致檢測失靈等問題。
超聲探頭檢測法是一種直接將超聲收發探頭放入待測鋁合金熔體中檢測夾雜物的方法。檢測系統主要由信號發射器、信號接收器和信號處理器等幾部分組成。當超聲波在熔體中遇到夾雜物時,部分聲束被反射導致超聲波能量衰減,通過對比發射和接收的超聲波振幅變化,即可判定夾雜物的尺寸和數量。
探頭材料和結構是熔體夾雜超聲檢測的關鍵技術。國際著名鋁業公司肯聯鋁業為解決超聲探頭潤濕性和耐用性問題,采用創新技術研制了一種潤濕性更好的波導管,可保證超聲信號傳播更穩定,探頭實物照片如圖12所示。
Reynold s 金屬公司開發的一種熔體監控器Reynolds 4-M SystemTM,采用鈦合金制作探頭,探頭前端裝有口形諧振器,熔體可注滿或流過諧振腔,探頭結構簡圖如圖12所示。超聲探頭發出的超聲信號穿過腔內熔體,遇諧振腔底平面反射回熔體又被探頭接收并送信號處理單元處理,可同時完成衰減變化率、縱波速度測定和反射脈沖頻譜分析及缺陷識別,可探測尺寸為超聲波長1/2的懸浮雜質顆粒。
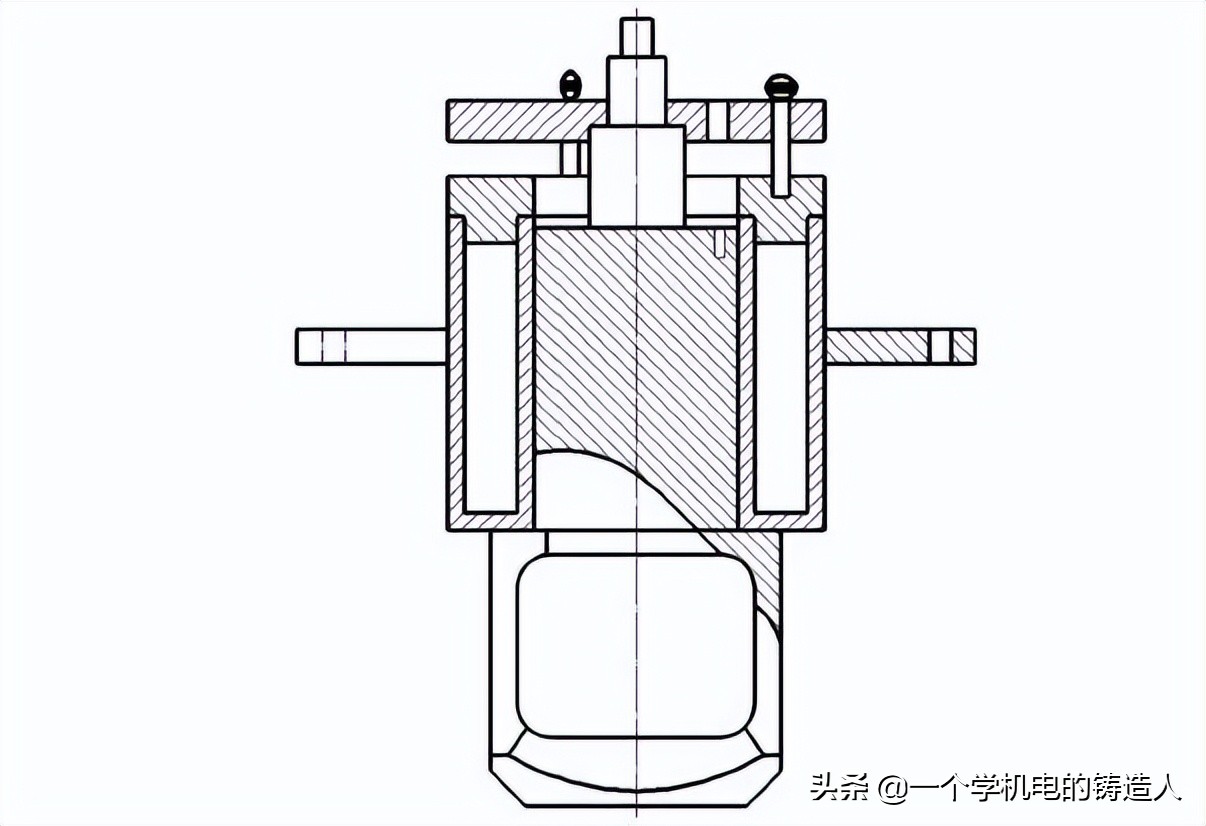
圖12 Reynolds 4-M SystemTM探頭結構簡圖
Hudson等人通過實驗驗證了用LIBS技術對鋁熔體夾雜檢測的可行性,將氣泡吹入液態鋁中,隨后加入干凈金屬,發現氧的光譜強度隨熔體潔凈度而變化,說明LIBS技術可以區分熔體的相對潔凈度。Hudson還用純鋁熔體中加入SiC顆粒作了類似的實驗,得到了SiC體積分數低于0.006%時(類似于氧化夾雜的濃度),Si信號平均強度和SiC體積分數成線性關系。
在已知樣品體積和顆粒中元素濃度時,Hahn等人還推導出了顆粒尺寸的表達式。因此,夾雜顆粒尺寸大小原則上可以通過計算每次激光測試中氧信號的強度來確定。
1.4 合金熔體結晶性能預測
通過特制小試樣類比鑄件凝固過程觀察,不僅可以預測熔體結晶后的金相組織和力學性能,還可評價合金鑄造性能。除此之外,借助合金熔體某些熱物性參數檢測,亦可實現熔體結晶組織快速預測。
1.4.1 合金結晶組織爐前快速觀察
三角試片觀察法快速判定鑄鐵含碳量和白口傾向是最原始的爐前快速檢測方法,因簡單快捷、成本低廉,目前依然被許多企業采用。
日本中山株式會社生產的NAP-2型球鐵組織快速分析儀,可在6min內自動完成制樣、粗磨、拋光、照排、分析全過程。該儀器一次最多可放5個試樣,切斷和研磨均為干式法,研磨精度符合金相要求,放大倍數為100倍,球化判定分析方法采用JIS和NIK方法,取10個視野平均值表示,結果可存儲,并可通過USB口拷貝分析結果。
1.4.2 合金結晶組織性能熱分析預測
我國鑄造熱分析技術集中引進和自主研究開始于20世紀80年代前后,當時代表性國外熱分析儀品牌主要有德國、比利時、日本等產品。國內有關企業、研究院所、高等學校等先后開展了各類熱分析儀開發研究,上海柴油機廠、徐州機械研究所、天津機械研究所、沈陽工業大學、清華大學、上海交通大學、哈爾濱工業大學、哈爾濱科技大學等都有熱分析儀產品推出和研究成果發表。
鑄造合金熱分析是一種基于合金熔體凝固過程潛熱分析相變化進而實現組織性能預測的快速檢測技術。因此,決定熱分析儀水平高低的關鍵是熔體冷卻曲線特征值的精準測定和特征值與預測參數之間內在聯系的準確描述。前者依賴取樣器性能穩定和特征值可靠識別,后者依賴機內預存數學模型的可信度和實用性。多年來,國內外鑄造工作者在取樣器結構設計和數學模型建立方面開展了大量創新性研究工作。
熱分析取樣器即熱分析樣杯可分為冷取樣(等待樣勺澆樣)樣杯和熱取樣(直接浸入熔體取樣)樣杯兩大類,還可依據杯體材料、杯體形狀、熱電偶結構等特點進行細分。幾款目前常用的熱分析樣杯如圖13所示,圖13a方形平偶石英管保護砂型杯為比利時熱分析儀配套樣杯,圖13b圓形立偶陶瓷管保護為多款儀器配套樣杯,圖13c雙球平偶石英管保護砂型杯為OCC熱分析儀專用杯,圖13d倒立偶陶瓷管保護金屬型為辛特卡斯特熱分析專用杯。圖13a-c為冷取樣樣杯,圖13d為熱取樣樣杯。
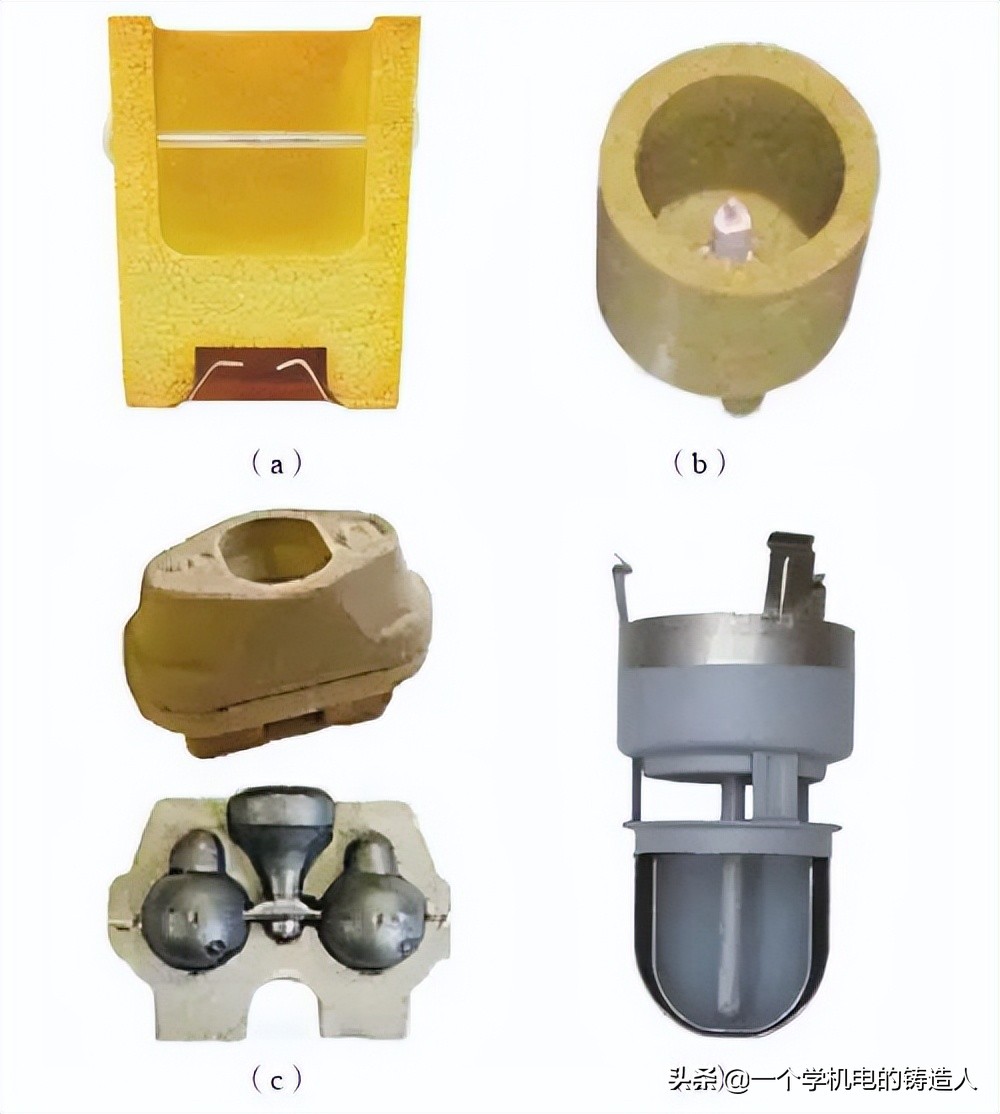
圖13 幾種典型熱分析樣杯實物照片
熱分析樣杯結構和材料的變化,從一個側面反映了熱分析技術的進步。13a-b是最早應用的樣杯,圖13c-d是后期改進的樣杯。從熱分析工作原理上分析,冷卻曲線形狀受樣杯及試樣與環境之間熱交換的影響,定量取樣和恒溫澆注是穩定熱交換條件的最好做法。從這個意義上說,圖13c-d兩種樣杯的穩定性更高。當然,兩種專用樣杯還有其他特殊考慮,包括內覆特殊涂層和熱電偶布局等也特別重要。
在準確采集熱分析信息參數的前提下,熱分析數學模型的實用性取決于模型特征值選取的科學性和所建模型的適應性。合理選取特征值有賴于建模者對合金熔體凝固過程熱力學及動力學的深入理解,提高模型兼容能力的途徑正隨AI技術的進步在不斷拓寬。熱分析方法最初引入鑄造,只是依據冷卻曲線判定鑄鐵含碳量及碳當量,特征值是液相線溫度TL,后來拓展為測定硅含量,通過向樣杯加入反石墨化元素Te改變鐵液凝固方式獲得穩定特征值Ts。再后來人們又發現共晶凝固階段的最低溫度Teu、最高溫度Ter、過冷度△T、結晶時間△t等多個特征參數與鑄鐵結晶組織及力學性能的關聯性,由此誕生了多種形式的熱分析預測鑄鐵石墨形態、基體組織、力學性能的數學模型。
華中工學院熊國慶等于20世紀70年代末發表熱分析法測試球墨鑄鐵球化率的研究成果,綜合分析試驗所得近250條曲線,繪制Teu、△T2與球化率關系圖表,獲得了分三級評價球化級別的熱分析判據。美國阿拉巴馬大學Stefanescu D M教授曾于80年代給出了如圖14所示的球墨鑄鐵、蠕墨鑄鐵、灰鑄鐵和白口鑄鐵的凝固冷卻曲線]。哈爾濱科學技術大學孟繁玉等曾于80年代中期開展熱分析法預測鑄鐵共晶團數和力學性能的研究],北京工業大學李冬琪等在同期開展了微機化鑄鐵力學性能快速測試系統的開發工作。這些早期的研究成果對后期不斷擴大熱分析的功能起到了重要的推動作用。
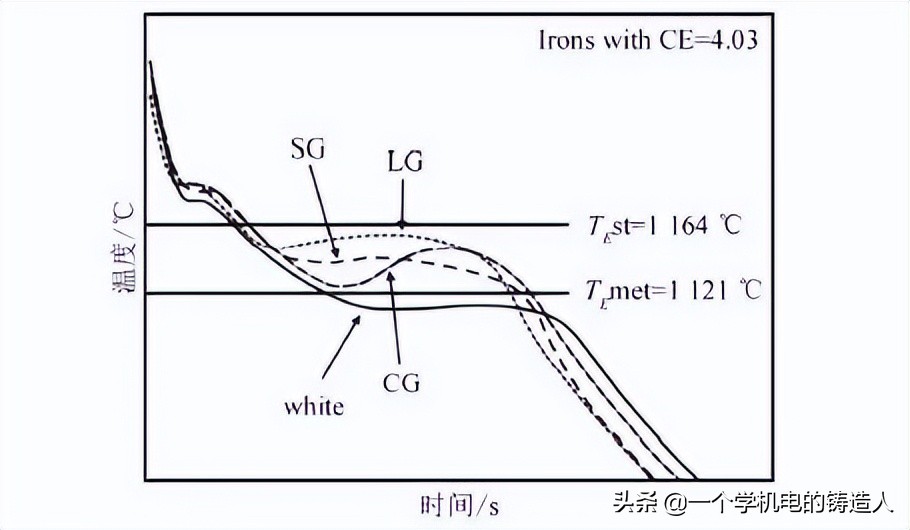
圖14 四種鑄鐵冷卻曲線
為了從不同角度觀察試樣凝固行為,以更準確地預測鑄鐵組織性能,日本菅野利猛于2000年開展了三樣杯同步測試研究,一杯用于獲得普通冷卻曲線,一杯用于獲得加碲白口曲線,一杯用于獲得加硅鐵合金孕育曲線,利用多曲線多特征值預測鑄鐵石墨形態和力學性能,可在同一坐標系下直觀顯示三條冷卻曲線,如圖15所示。
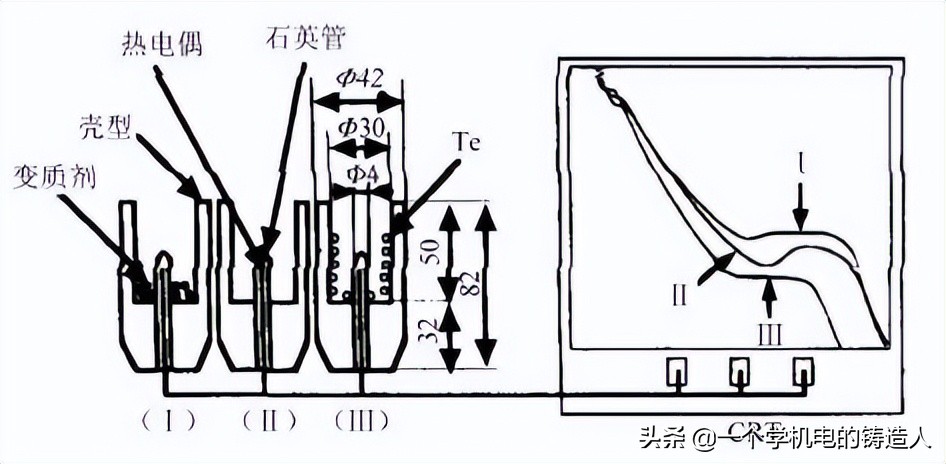
圖15 三樣杯同步熱分析及三曲線同步顯示
多樣杯取樣的熱分析方法已經作為成熟技術在鑄鐵生產中推廣應用。德國OCC蠕鐵蠕化處理控制系統采用一只普通加碲樣杯測定碳當量及含碳量,兩只雙球樣杯分別測定鐵液孕育指數和鎂指數,兩指數均位于蠕鐵區方視為鐵液合格。河北工業大學劉金海等研制的蠕鐵蠕化處理智能控制系統,利用三樣杯同步采集鑄鐵化學成分、過冷度、再輝溫度等特征值,實現蠕化兩步處理的優化控制。
熱分析法用于鋁合金、鎂合金的晶粒細化預測,是Kurfman于1961年首次提出的]。鋁合金熱分析用取樣器與鑄鐵熱分析相同,此外還有可重復使用的薄壁不銹鋼涂料樣杯,一款德國產MK鋁合金熱分析儀及配用不銹鋼樣杯和現插式熱電偶取樣裝置如圖16所示。
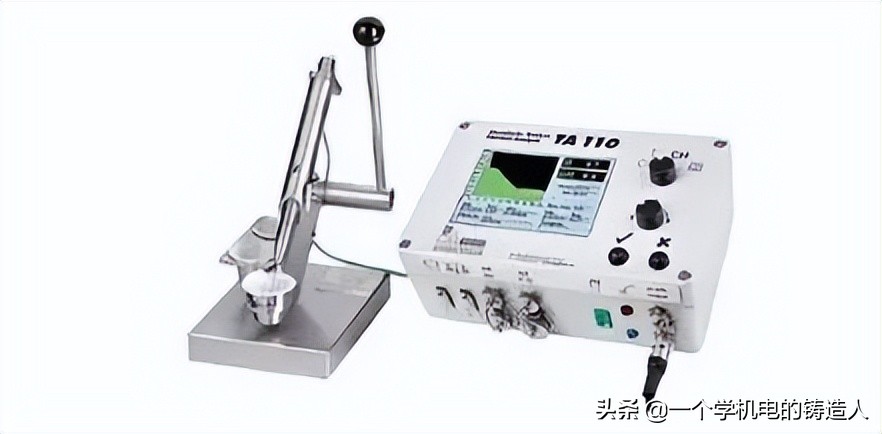
圖16 不銹鋼樣杯及現插式熱電偶取樣裝置
20世紀70年代開始,大量有關鋁、鎂合金晶粒度或枝晶間距與冷卻曲線特征值內在聯系的研究先后展開。迄今為止,建立鋁、鎂合金晶粒細化預測模型被采用最多的冷卻曲線特征值是初晶過冷ΔTl、共晶最低溫度Tu、共晶再輝溫度TR、共晶過冷溫度ΔTE和共晶時間Δt等。
D. Apelian等人研究了Al-7%Si合金的晶粒尺寸和初晶過冷度ΔT之間的關系。研究發現當過冷度ΔT較大時,晶粒尺寸也較大;當ΔT<0.3℃,合金的晶粒尺寸較小。Ananthanarayanan等人研究了319合金,結果表明, 過冷度ΔT受多種因素的影響,如冷卻速度、合金元素的含量等。冷卻速度和合金元素含量越高,ΔT越大,因此,只用初晶過冷度還不足以表征熔體的細化處理效果。隨后D.Gloria等人同樣研究了該合金,發現初晶過冷再輝時間Δt比過冷度ΔT能更好地評價晶粒大小,晶粒越細小,過冷再輝時間Δt也越小。Najmeddin等人研究了4種細化劑對A356合金細化效果的影響,研究發現細化劑對凝固溫度、凝固時間和潛熱無顯著影響,當形核的最大過冷度≤3.8℃時,合金的細化效果最好。
國內鑄造工作者哈爾濱工業大學林海峰、郝啟堂、華中理工大學吳樹森等都先后開展了鋁合金熱分析研究,認為樣杯對熱分析曲線特征值有很大影響,熱分析曲線特征值ΔTG、ΔTEG可分別作為初晶Si、共晶 Si 變質效果的判據。
郝啟堂等提出兩種判定晶粒度的方法,一是過冷面積,認為它同時反映了形核過程中的過冷度和過冷時間,過冷面積越大晶粒越粗大;過冷面積越小晶粒越細小;二是固相生長加速度,固相生長加速度小,表示初生相一開始形核便具有很大的形核速度,亦即形核率從小到大的過渡過程比較短,此時合金具有較細的晶粒。反之,固相生長加速度大,表示初生相開始形核時速度較小,只有過冷進一步減小,形核速度才能逐漸增大,此時晶粒則比較粗大。
由于變質處理和細化處理是兩個不同的概念且具有不同的晶粒細化機制,熔體結晶過程中的潛熱變化反映在冷卻曲線上的特征值變化具有特殊的含義。
M. Djurdjevi等人研究了不同Sr含量對319合金變質效果的影響,通過熱分析曲線發現加入Sr變質時共晶硅的生長溫度明顯降低,變質前后共晶生長溫度變化(ΔT)與變質效果等級之間存在一定關系。因此,可以通過共晶生長溫度變化預測鋁硅合金的變質程度。Malekan等人采用熱分析法研究了Al-5Ti-1B細化劑和Al-10Sr變質劑對319鋁合金凝固特性和組織特征的影響,通過對比319鋁合金變質處理前后的冷卻曲線,發現鋁硅共晶生長溫度ΔTG,E可用于預測鋁硅合金的變質效果。Zamani等人研究了不同Sr含量和不同冷卻速率對Al-Si合金共晶區的影響。隨Sr含量的增加,變質前后生長溫度變化(ΔTG)與抗拉強度趨勢相一致,與冷卻速度無關。隨共晶生長時間(Δt)的延長,合金的拉伸性能也呈現出相似的變化趨勢,但不同冷卻速率下趨勢不一致。
北京航空材料研究所龔磊清研究了ZL104合金的變質效果,認為單獨使用變質前后共晶生長溫度的差值(ΔTE)評價變質效果不夠全面,同時參考共晶生長期(te)。當變質前后共晶生長溫度的差值>10℃和共晶生長期>110s,合金的變質效果更好。王英杰等人對ZL101A合金變質效果的研究發現,變質前后共晶生長溫度的差值>8℃和共晶生長期>90s時,合金的變質效果更好。
熱分析冷卻曲線被稱為合金的冶金指紋,熱分析建模方法除建立冷卻曲線特征值與預測參數之間數學或數字關系外,另一條有效路徑是冷卻曲線形狀比對,即通過大量試驗,同步獲取不同試樣的冷卻曲線及其金相組織、力學性能等信息參數,存入計算機數據庫用作熱分析測試的比對標準樣本。現場測得合金冷卻曲線后,自動進入數據庫與預存樣本逐一比對,以冷卻曲線形態最相似者的綁定數據作為檢測結果。清華大學李言祥等就此做過系統研究,生產試測證明方法可行。筆者認為,模型準確性取決于數據庫數據的代表性,隨著數據庫樣本量的不斷豐富,相似度比對方法的不斷進步,不僅預測精度可以更加提高,預測參數還可更加寬泛,相似度比較法是一種頗有應用前景的好方法。
熱分析與其他現代技術相結合,構建多維檢測系統也是充分發揮其優勢的重要方面,日本鑄造服務株式會社安田敬司在2019中國鑄造活動周上交流的ATASMetStar自適應熱分析系統就是一例。將可輸出38個參數的ATAS MetStar與光譜儀結合,進行鐵液高精度CE值管理,可將TL控制在±2℃;將ATAS MetStar與喂絲和隨流孕育設備相連,可根據鐵液狀態控制球化處理,使工程完全自動化;通過IOT(物聯網)將鐵液品質數值化、數據化及可溯化,可使工程管理更加容易。
深入挖掘合金熔體凝固過程的其他物性參數變化,借助人工神經網絡等AI工具,建立可測信息參數與凝固組織及性能的關系,實現鑄件質量的多方法爐前快速預測,是熔體質量爐前快速檢測技術的重要研究方向。
1.4.3 合金鑄造性能檢測
合金鑄造性能包括流動特性和凝固特性,鑄造性能的準確測定對于開發新型合金材料和設計鑄造工藝具有重要意義。
(1)合金熔體流動特性檢測。目前,鑄造企業及高校鑄造實驗室仍多采用螺旋試樣測定合金熔體流動性,即以漸開線形狀螺旋線流長表征被測合金熔體流動性。在固定澆注溫度和鑄型材料及溫度的條件下,檢測結果具有可信性。為了獲得更多熔體流動信息,哈爾濱理工大學鑄造測控技術研究室開發了一種可視化熔體流動特性檢測裝置。如圖17所示,檢測裝置由干砂型、耐熱玻璃、澆口杯(帶塞桿)、攝像頭和計算機數據采集單元組成。取待測合金熔體定量澆入澆口杯,熔體溫度降至約定值時提拉塞桿,熔體流動過程中計算機數據采集單元實時采集試樣流長信息,并動態計算實時流速和流長,最終輸出流動性檢測結果。
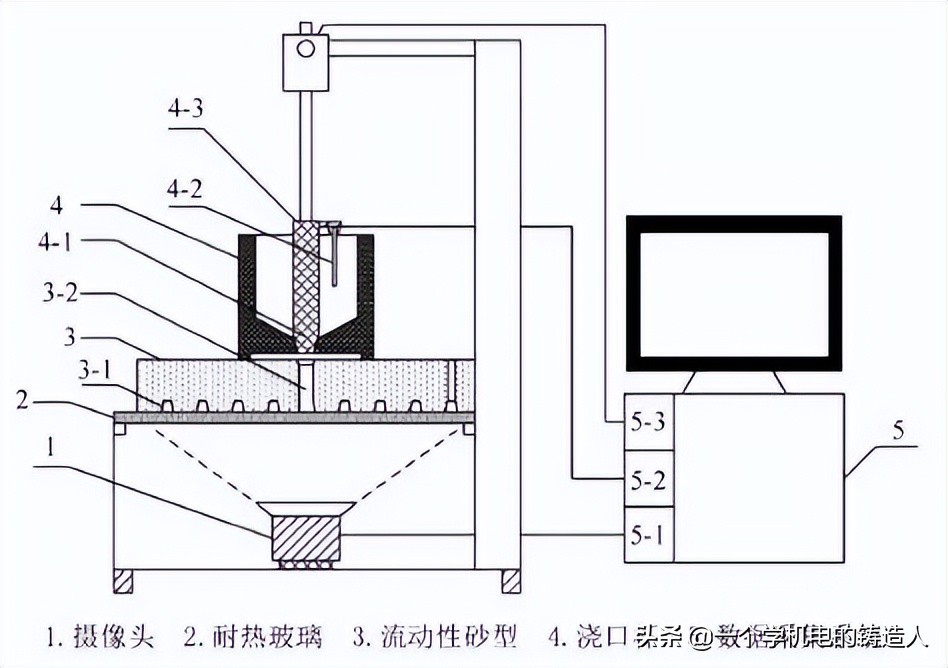
圖17 熔體流動性可視化檢測裝置構成簡圖
(2)合金熔體凝固特性檢測。20世紀70年代,原大連工學院鑄造教研室開發了鑄造合金線收縮、熱應力及熱裂傾向檢測儀,采用X-Y記錄儀記錄合金試樣凝固過程線收縮量、應力和溫度變化。進入新世紀后,哈爾濱理工大學鑄造測控技術研究室開始研制合金凝固特性新型檢測裝置。新型檢測裝置采用滑輪移動和蝸輪蝸桿等特殊機構,使試驗裝模和卸載更加便利,計算機實時采集試樣凝固過程應力、溫度、位移信號并存儲,測試結束后可以三參數中任一參數為索引調用同時刻另外兩參數。新型凝固特性檢測裝置實物照片如圖18所示,從2013年開始,新型凝固特性檢測裝置已在部分高校和企業鑄造實驗室使用。
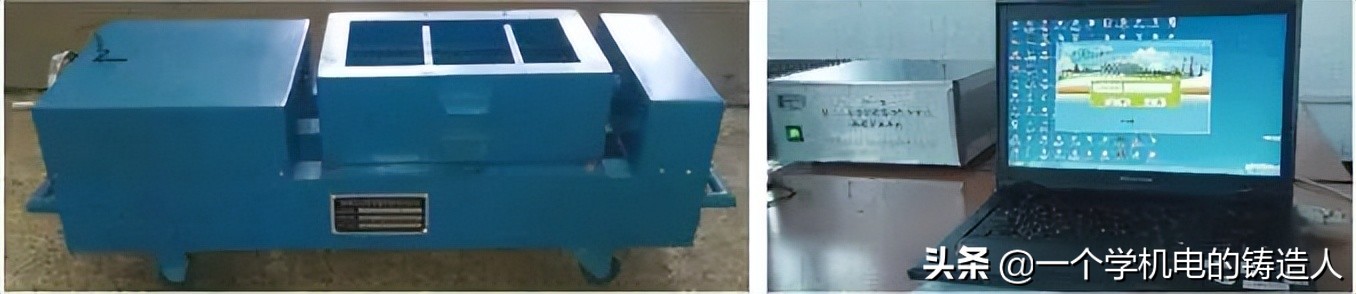
圖18 鑄造合金凝固特性新型檢測裝置
2 濕型粘土砂及砂型質量檢測技術
濕型粘土砂鑄造依然是目前最主要的鑄造方法,型砂質量是影響鑄件質量的主要因素之一。據統計,在鑄造生產中有60%的鑄件廢品源于型砂質量和砂型質量。在混砂和造型工藝穩定的條件下,型砂及砂型質量取決于型砂組分和性能。因此,及時發現和有效控制型砂組分及性能的變化,對于穩定砂型質量至關重要。本節重點介紹濕型粘土砂和砂型質量檢測技術研究及應用進展。
2.1 濕型粘土砂質量檢測
濕型粘土砂主要由原砂、粘土、水及煤粉等原輔材料組成,生產中對型砂原材料質量及配比均有嚴格要求,通過適時添加新料和階段性廢棄舊砂保持型砂組分相對穩定。
2.1.1 濕型砂原材料質量檢測
(1)原砂粒度檢測。原砂粒度是指砂子顆粒尺寸及大小顆粒之間的比例,它對型砂透氣性、耐火度及鑄件表面質量均有影響。生產中一直采用標準篩配擺動式或震擺式篩砂機測定原砂粒度,標準篩由11個篩框(6目至270目)疊螺組成。取50g原砂洗凈烘干后放入頂層篩框,啟動篩砂機篩分15min,精確稱量每個篩框上的存余砂重,采用三篩號表示法或平均細度法等方法表征粒度,上述動作均由人工完成。實踐表明,耗時長和稱重要求高是篩砂機篩分法的明顯不足。多年來,有關原砂粒度檢測方法和裝置研究的新成果尚不多見。
日本鑄造工作者開發的RT-200型全自動原砂粒度測定儀是一款集篩分、稱重、清理、顆粒組成計算和分析為一體的儀器,篩分系統由8個篩子和底盤組成,通過振動系統篩分后,由稱重系統計量每一篩框上型砂重量,再由計算分析系統計算出顆粒組成。檢測過程分四步,第一步,固定篩子;第二步,投放砂樣;第三步,震擺篩分;第四步,稱重清掃。分析系統除了可以給出粒度組成外,也可將生產所要求的原砂粒度條件與測試結果進行比較,從而判斷所測原砂是否滿足生產要求。
近年來, 激光粒度分選已在玻璃、電纜等許多生產領域獲得成功應用。Microtrac Retsch開發的CAMSIZER P4顆粒組成自動分析儀,利用雙攝像機技術采集自由落體運動過程中的顆粒圖像,通過圖像識別分析顆粒大小和形狀,可測試范圍為20μm~30mm,首先,小機械手將裝有原砂樣本的樣筒夾緊并翻轉,將原砂倒入到集砂器內,原砂從集砂器流出后由振動流槽將原砂均勻地送入測試區,原砂在測試區中自由落體,光源照射在原砂上,所形成的背影由攝像系統實時采集并分析。CASMIZER P4每秒鐘可采集分析60幀圖像,因此其顆粒組成分析時間通常小于3min,且結果與傳統篩分方法吻合。CASMIZER P4的測試范圍及功能適合鑄造用砂的常規顆粒組成分析,可直接應用或適當改進后采用。
圖像識別及人工智能技術的不斷發展,為應用照相法實現原砂粒度快速分選創造了條件,相關研究工作已有開展,相信不久將來還會有更多粒度分選新技術出現。
(2)原砂含泥量檢測。泥和砂以顆粒大小區分,以直徑0.022mm為界,小者為泥,大者為砂。原砂含泥量是指原砂中直徑小于0.022mm的細粉物的質量百分數。
傳統測定原砂含泥量在洗砂機和洗砂杯上進行,稱取50 g烘干后原砂放入洗砂杯,加入285mL水和15mL濃度為1%的NaOH,啟動洗砂機攪動洗砂杯內水砂混合物10min,加清水至指定刻度,靜止8min,用虹吸管吸走上部渾濁水,再次加清水、靜止、虹吸直至水清,烘干杯底砂粒、稱重并算得含泥量。
戴慧珍曾于1975年發表建筑用砂子含泥量免烘干快速測定方法。吳毅于1987年發表該方法用于鑄造新砂含泥量檢測的試驗結果]。免烘干檢測方法的工作原理是向燒杯加入定量待測新砂,進行三次加水、渦洗、排泥循環,每次計量排泥后混合體重量,最后利用公式計算原砂含泥量。
哈爾濱理工大學鑄造測控技術研究室,基于濁度傳感器開發了一種免虹吸、免烘干原砂含泥量快速檢測方法是采集渦洗后泥漿沉降過程中關鍵時間節點液體濁度,經分析計算給出含泥量參數。經進一步改進,免虹吸、免烘干檢測裝置有望用于鑄造型砂含泥量檢測。
粘土吸藍量檢測。粘土的礦物成分是區分其種類和質量的有效方法。一般而言,粘土含蒙脫石75%以上稱為膨潤土,蒙脫石含量越高,膨潤土質量越好。由于粘土礦物具有吸附色素(如苯胺染料、甲基紫、亞甲基藍等)的能力,尤以亞甲基藍吸附量較大。通常采用染色法測定蒙脫石含量,每100g干蒙脫石約能吸附44g亞甲基藍,以每100g膨潤土吸附亞甲基藍的克數除以0.44即為被測膨潤土的蒙脫石百分含量。
依據亞甲基藍滴定終結識別方法的不同,染色法測定蒙脫石含量可分為目測法和儀器比色法。為簡便起見,實際鑄造生產中常用滴定濾紙光暈識別方法判斷滴定是否到位。目前,裝有計算機識別系統的儀器比色法膨潤土分析儀已有商品推出。
2.1.2 濕型砂組分檢測
砂、土、水構成濕型粘土砂三大骨干組分,控制合適的水分含量和有效粘土含量是砂處理系統的主要任務。無論是基于組分檢測的直接調控系統還是基于性能檢測的間接調控系統,實質調控參數均為含水量及有效粘土含量。為此,需要在線快速檢測舊砂含水量及有效粘土含量,以確定每次混砂組分配比。
(1)水分含量檢測。型砂中的水分一般指在105~110℃以下烘失的水分。型砂水分的標準檢測方法是烘干稱重法(GB/T2684—2009標準),但其因耗時過長難以在線應用。為了滿足快速檢測的需要,多種間接快速測濕方法先后應運而生,其中有代表性的檢測方法有成型性法、電阻法、電容法、電感法、紅外吸收法和微波吸收法等。
成型性法只能用于控制型砂水分,通過型砂穿越狹縫的能力判斷含水量是否處于預控范圍,20世紀70年代前后有較多應用,后來被其他測濕方法取代。
湖北省機電研究院馮勝山基于電阻法研制了SJZJ-1型數顯便攜式造型材料水分快速測定儀,配用鉗式和針式傳感器,可測8種型砂材料水分,檢測誤差±0.2%~0.4%,檢測時間不超過30min。大連鐵道學院劉趙銘等從理論上分析了極化作用的影響因素,對極板面積、激勵電源頻率及電壓進行了試驗研究,證明降低激勵電壓、加大極板面積和采用交流電源激勵有利于減弱極化影響。東華大學朱世根等研制了超高頻電容式型砂水分傳感器,實驗結果證明,當電源頻率達到30MHz時,型砂水分測試上限可以達到10%以上。天津大學李貴成研究了平衡互感電橋法測試型砂水分的可行性,采用有機玻璃制作圓盤線圈骨架,其上分別纏繞三組線圈,線圈1、3反向連接后由1000Hz音頻電源供電,線圈2接入放大電路,信號經整流、濾波后送顯示儀表顯示檢測結果,互感電橋測試結果與烘干法比較相對誤差不超過5%。吉林大學碩士研究生葛曉雷研制了基于近紅外光譜分析的型砂水分測量儀,試驗表明水對1.94μm波長紅外線吸敏感度更高、線性度更好。武漢工業學院張永林等研究設計了基于微波透射原理的型砂智能水分測量系統,采用全固態高可靠性微波功率源(10GHz),消除了型砂密度、成分、形狀對測量的影響,測水范圍0~10%,重復性誤差小于±0.2%,測量速度10次/s。近期,波蘭Wroclaw科技大學的Beata Gal等發表其濕型粘土介電特性微波檢測試驗研究結果,采用2.45 MHz微波測定濕型粘土砂介電常數,證明相對復數介電常數與粘土及含水量成正比,與強度成反比,利用濕型砂介電常數檢測含水量及濕壓強度具有可行性。
目前,國內外型砂質量監控系統多采用電容或電阻式傳感器測定水分。紅外吸收和微波吸收測試方法雖然具有非接觸檢測的顯著優勢,但其設備復雜性及成本遠高于電阻、電容法。日本新東公司研制的MIC型砂水分測試儀以交流電阻法為原理,用于測定舊砂的含水量,同時將熱電偶安裝在傳送帶上測量舊砂的溫度。德國LIPPKE公司采用電容法開發了FS-2型含水量測量裝置,在混砂機或冷卻器上的出入口處安裝傳感器獲取含水量,舊砂含水量測試范圍為0~3.5%,精度為±(0.2%~0.3%)左右。
(2)有效粘土含量檢測。舊砂及混制砂有效粘土含量在線快速檢測技術目前尚處于試驗研究階段,不同方法在檢測速度和準確性提高方面還有許多工作要做。
華中科技大學博士研究生龍威在其粘土砂有效膨潤土自動測定方法及質量控制系統研究博士論文中,完成了基于計算機圖像識別技術的舊砂有效粘土含量自動測試方法研究,利用淡藍色和深藍色的A/G/B三通道感光程度差別,將彩色滴斑圖像分解為三通道灰度圖像,并對其進行灰度值減法運算、灰度變換、閾值分割、提取外圈淡藍色暈圈和內圈藍斑,計算外圈淡藍色暈圈和內圈藍斑面積,當內圈藍斑與外圈淡藍色暈圈的面積比值達到設定值15%時視為滴定終結,系統自動計算吸藍量值和有效粘土含量。
利用濕型粘土砂在直流電場作用下表現出的極化現象,哈爾濱理工大學鑄造測控技術研究室于1995年首次提出雙電源二次激勵法快速測定型砂有效粘土含量。雙電源二次激勵法基本原理是,在直流電場作用下,型砂中的陰、陽離子會向正、負電極移動并在極板附近聚集,結果導致與外電場方向相反的附加電場建立,宏觀上表現為外加電場強度被削弱,外電場強度削弱程度與型砂水分和膨潤土種類及含量等因素相關,這就是所謂的極化作用。雙電源二次激勵法的目的在于通過對被測砂樣交、直流電源兩次激勵,實現水分與膨潤土對極化效果影響的分離。但由于極化過程比較復雜,僅用交、直流壓降等簡單信息參數很難求解型砂含水量和有效粘土含量。近期研究證明,采用極化進程中更多的導電特性參數輔以緊實率等參數作為輸入參數,選取恰當的人工神經網絡進行學習訓練,有望獲得更好的測試結果。
2.1.3 濕型砂性能檢測
濕型粘土砂性能分常溫性能和高溫性能兩大類,生產現場一般只檢型砂常溫性能,常檢性能指標主要有緊實率、濕強度和透氣性,相當數量的鑄造企業砂處理系統只以緊實率為監測指標。型砂性能檢測裝置可以是便攜式檢測儀器或在線檢測系統。目前,特別成型的便攜式檢測儀器還不多見,應用相對較多的是固定式或移動式在線檢測裝置。
(1)在線自動檢測裝置。基于對濕型粘土砂組分與性能關系及控制理念的不同認識,在線檢測參數確定原則會有很大區別。繼20世紀60年中期,美國HarryW.Dietert在AFS Transactions上發表用同一試樣檢測型砂水分、溫度、緊實率、透氣性、濕壓或剪切強度和濕壓變形的型砂自動測試儀研究成果之后,80-90年代,是國外先進鑄造檢測裝置集中推出時期,也是我國鑄造工作者研究開發鑄造型砂性能在線檢測裝置的高峰時期。
清華大學黃天佑教授在《鑄造》雜志(1996.6)發表論文中,詳盡地介紹了德國Eirich公司的Qualimaster、FoundryControl公司的SPC(Sand ProcessControl)、ME(Minchenfeld Elektrotechink)公司的Sandlab、瑞士GF公司的SMS(Sand Multi controller、日本早坂理工株式會社的MIE、太陽鑄機株式會社的KCB以及美國Hartley Controls 公司的2500系列型砂性能在線檢測儀的功能特點。德國Qualimaster在線檢測儀在送砂皮帶上直接取樣,與計算機專家系統軟件配合使用,實現對砂處理的預防性質量控制。SPC為轉盤式多工位型砂質量在線檢測儀,皮帶直接取樣,可測緊實率、含水量和砂溫,通過計算機與Lippke水分控制儀配合實現型砂質量控制。Sandlab儀器亦為送砂皮帶直接取樣,可檢測緊實率、剪切強度、變形量等參數,與混砂機和雙盤冷卻器的測溫、測濕及自動加水系統配合實現型砂性能控制。瑞士SCC型砂緊實率測定儀是世界上最早的型砂在線檢測儀,1994年參展的SMS型砂在線檢測儀,由螺旋取樣器從混砂機側孔取樣送入儀器檢測緊實率和抗壓強度。日本GTR儀器與瑞士GF公司產品類似,但采用手工取樣,檢測項目包括砂溫、緊實率、含水量、透氣性和抗壓強度。MIE儀器從混砂機側孔取樣,檢測參數包括緊實率、水分和砂溫。KCB儀器只檢測型砂緊實率,用于混砂機加水量控制。美國2500系列亦為型砂緊實率自動檢測儀,皮帶直接取樣,與混砂機用水分及砂溫測濕裝置配合使用實現加水量自動控制。
國內方面,20世紀80年代初期,機械工業部第六設計院黃祖裘等推出一款型砂三性能自動檢測儀,檢測參數包括含水量、透氣性和濕壓強度。采用電容法分兩段(0~3.5%/13.65MHz;4.0%~7.0%/3MHz)檢測型砂水分,采用100mmH2O恒壓氣源檢測透氣性,采用壓頭串接壓力環測定濕壓強度。80年代末期,東南大學王祥生等推出濕型粘土砂五性能自動檢測儀,檢測參數包括型砂水分、溫度、緊實率、透氣性和劈裂強度。型砂水分采用直流電阻法檢測,透氣性采用鐘罩自由下落排氣法測定,檢測周期大約1min。90年代初期,華南理工大學陳紹華等推出濕型砂三性能快速檢測儀,檢測參數包括緊實率、濕壓強度和透氣性。透氣性亦采用鐘罩自由下落排氣法測定。三參數檢測周期約定為1.5min。90年代中末期,清華大學吳俊郊等與企業合作推出一款C1814型砂性能自動測控儀,立足結構簡單、可靠實用,只檢測緊實率和濕壓強度兩項指標。儀器機械結構簡圖如圖19所示,數據處理采用PLC完成。
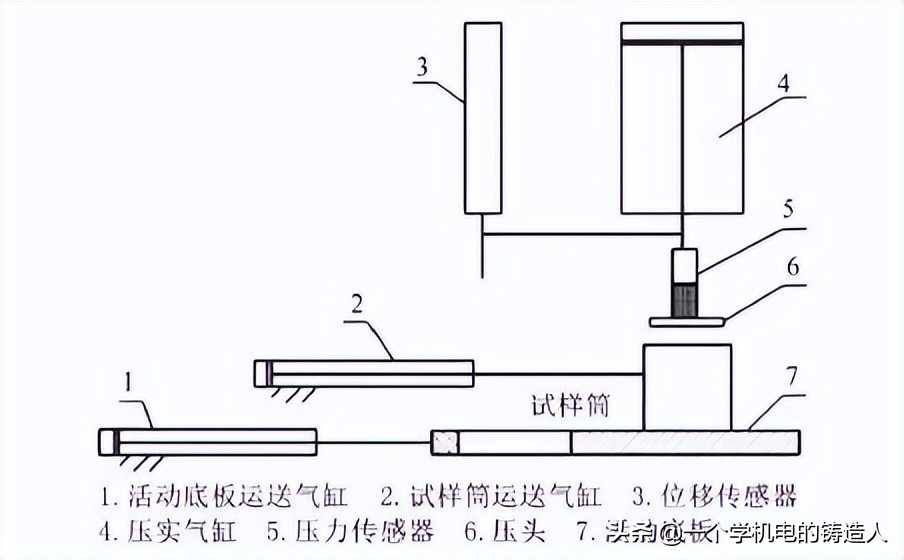
圖19 C814型砂自動檢測儀結構簡圖
進入新世紀,基于緊實率和濕強度檢測的濕型砂質量控制系統日趨成熟。國外品牌裝備除DISA、GF、Eirich、新東等不斷有更新換代以外,其他國外產品也在陸續推出。新東IDST型砂在線檢測儀,可在線檢測濕壓強度、水分、透氣性、砂溫和活性粘土含量(計算值)。印度VEP(Versatile Equipments Pvt. )公司生產的VCAT-II在線型砂檢測儀,檢測參數包括緊實率、水分、相對透氣性和砂樣強度。該儀器既可用于在線測試亦可在型砂實驗室使用,將砂樣放入集砂口,即可自動測試其緊實率、水分、相對透氣性和砂樣強度。
國內研究開發的幾種濕型粘土砂在線檢測裝置基本以緊實率為核心參數,配測濕壓強度,重在以優化的控制策略完成混砂全程控制。濟南鑄造鍛壓機械研究所自主開發了CB1型砂在線緊實率控制裝置。該裝置由緊實率在線檢測儀和加水系統組成,包括提料裝置、取料裝置、推刮壓實裝置、吹氣清理裝置及機架幾部分。通過取樣、松砂、刮平、壓實等工位完成緊實率檢測,在線循環檢測最小周期為14s,檢測緊實率精度為±1%。常州好迪公司開發的SC型及法迪爾克產品RTC107型型砂在線檢測儀,均通過監測回用砂及混砂機內型砂溫度、緊實率和濕壓強度,實時調整加水量和膨潤土補加量。
便攜式檢測裝置。目前,便攜式型砂性能測試儀器主要是緊實率測定儀和透氣性測定儀或雙參數集成測定儀。
大連理工大學李劍中研制了一種便攜式型砂緊實率快速智能測試儀。采用人工加壓緊實型砂,壓力傳感器和位移傳感器配合記錄對應緊實力為P1和P2時的壓頭位移,經簡單計算可得被測型砂緊實率。
哈爾濱理工大學鑄造測控技術研究室,自20世紀90年代開始,先后研究濕型粘土砂透氣性和緊實率檢測新方法,并基于新方法和單片機及大規模數字電路開發了多款便攜式測試裝置。新方法采用定壓排氣計時方式測定型砂透氣性,配用彈簧自動恒壓制樣器,可在短時間內快速完成透氣性檢測,具有省時、便捷、準確的特點。進入2000年后,研究室開發了濕型粘土砂透氣性緊實率及鑄型緊實度集成檢測裝置,利用主輔雙樣筒制樣,采用定時測壓測定透氣性、二次加壓測定型砂緊實率和彈簧驅動沖頭測定砂型緊實度,證明多參數集成測試亦可在便攜式儀器上實現。
2.2 砂型質量檢測
砂型質量是型砂和造型質量綜合影響的結果,對工藝穩定的自動造型線而言,型砂合格亦可視為砂型合格,但對于工藝不穩定的造型機或處于調試階段的造型線或非自動化造型線而言,砂型質量現場檢測則非常必要。檢測指標主要包括砂型表面硬度、砂型緊實度和砂型透氣性。
2.2.1 砂型表面硬度檢測
由于砂型表面硬度在一定程度上可以代表砂型緊實程度,鑄造行業也多用表面硬度評價砂型質量。生產中常用的砂型表面硬度檢測儀器有指針式硬度計和數字式砂型表面強度計。指針式硬度計靠彈簧壓力與受壓砂型反作用力平衡時壓頭的壓入深度評價砂型表面硬度,根據不同砂型可選擇球形或錐形壓頭。數字式砂型表面強度計采用柱形壓頭貫入指定深度,內置微型壓力傳感器鎖存峰值貫入阻力視為砂型表面強度。
2.2.2 砂型內部緊實度測定
砂型緊實度檢測在造型方法及造型設備研究開發中具有重要意義。哈爾濱工業大學任天慶等,早在20世紀80年代初,基于靜力觸探原理研究砂型緊實度分布檢測方法,試驗得出探頭直徑及型砂性能與貫入阻力關系及不同直徑探頭的探測精度,證明靜力觸探方法可用于造型過程檢測]。清華大學吳俊郊等研究高緊實度砂型緊實程度評價方法。試驗表明,砂型硬度計或GF公司表面強度計通過測頭插入砂型表面一定深度可測得砂型強度,評價方法具有穩定性好、適用范圍廣、簡便易行的特點。
哈爾濱理工大學鑄造測控技術研究室開發了一種便攜式砂型緊實度數字化測定儀。采用靜力觸探桿串接半導體力傳感器檢測貫入阻力,配套貫入深度設定裝置,可以測定量程范圍內任意深度砂型內部緊實程度,探頭到達設定深度后,系統自動鎖存貫入阻力峰值,經計算轉換為緊實度參數。砂型任意深度緊實度測定裝置結構簡圖如圖20所示。
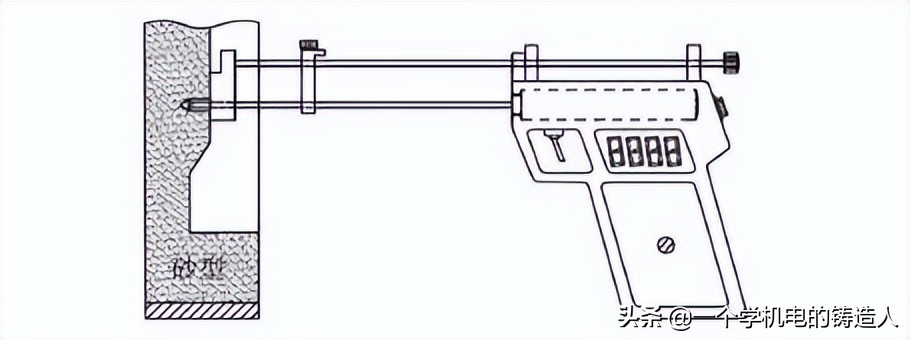
圖20 砂型任意深度緊實度測定儀結構簡圖
3 鑄件質量無損檢測技術
液態合金成形是一個復雜的過程,即使在熔體和鑄型全部合格的條件下,也不能保證所有鑄件全部合格。因此,對鑄件進行無損檢測十分必要。無損檢測技術是指在不影響鑄件質量和性能的情況下,利用鑄件材料內部缺陷引起的熱、聲、光、電、磁等物理參數變化,借助射線、超聲、紅外、電磁等技術及儀器對鑄件表面和內部缺陷的數量、尺寸、位置、分布等進行檢測的方法。常規無損檢測方法包括滲透檢測、磁粉檢測、渦流檢測、射線檢測、超聲檢測等。
3.1 鑄件表面質量檢測
3.1.1 表面缺陷檢測
鑄件表面常見缺陷主要有粘砂、夾砂、結疤、冷隔及非穿透型裂紋等,常用檢測方法包括目視檢查、滲透檢測、磁粉檢測和渦流檢測等。
(1)目視檢查。目視檢查是用肉眼直接觀察或借助器具目視檢查鑄件表面的一種宏觀檢測手段。近年來,隨著光電技術的進步,光纖內窺鏡、視頻探測鏡和工業檢測閉路電視等新型光電儀器日益走進鑄造車間,過去肉眼難以發現的細微缺陷和鑄件特殊部位(狹窄彎曲孔道等)的缺陷,得以清晰再現。
(2)磁粉檢測。磁粉檢測是利用磁化材料或工件表面的磁粉顆粒作為顯示介質對表面缺陷進行檢測的方法。鑄件被磁化后,缺陷部位將產生漏磁,磁粉在漏磁處出現聚集或定向,據此可判斷缺陷位置和性質。從20世紀50年代開始,我國先后引進前蘇聯、歐美等國家的磁粉檢測儀器,此后又自主研制了臺式和便攜式磁粉檢測儀,大大推動了磁粉檢測技術的應用和發展。由于磁粉檢測一般需要被測件表面預處理,鑄件在線連續檢測難以實現,但對線下鑄件進行表面裂紋檢驗時,磁粉檢測方法依然具有顯著優勢,配套鑄件表面預處理、勵磁和去磁及計算機圖像識別,可以構成鑄件裂紋磁粉自動檢測系統。陳新波等設計了一套智能磁粉探傷機,從移動磁化系統、移動夾緊系統,到噴液及回收系統操作全部集成在一個操作控制面板,可對大中型金屬件局部或整體進行自動磁粉檢測。李澤鑫等設計了一種便攜式磁粉探傷機,可對鑄件不同部位進行靈活移動檢測。
(3) 滲透檢測。滲透檢測是一種利用毛細管作用原理檢測材料表面開口類缺陷的方法。首先在材料表面缺陷處涂刷滲透劑并將多余液劑去除,在待檢測表面噴涂顯像劑顯現缺陷位置和形貌。國內外對滲透檢測方法、滲透劑使用及控制均有明確標準,美國滲透檢測代表了國際滲透檢測的一流水平,典型標準包括:ASTEM1417《滲透檢測的標準方法》、ASTEM165《滲透檢測的標準推薦操作方法》等。
我國滲透檢測方法采用的典型標準包括:國防科技工業軍事標準GJB2367《滲透檢測方法》、航空工業標準HB/Z61《滲透檢測》、特種設備行業標準JB4730《壓力管道無損檢測》等。同磁粉檢測一樣,滲透檢測多用于線下鑄件裂紋類表面缺陷檢驗,與計算機圖像識別相結合,構建滲透檢驗智能識別系統是今后研究開發的重點。
(4)渦流檢測。渦流檢測是基于電磁感應原理的一種非接觸式檢測技術,通過測定被測工件內部產生感生渦流的變化檢測缺陷。將通入交流電的線圈靠近或嵌入被測工件,線圈周圍的交變磁場使工件表面產生感生電流即渦流。當線圈在工件表面移動時,由于工件形狀、尺寸、缺陷、電導率等多種因素的變化,導致渦流分布和電流的大小發生變化并反作用于線圈,對于相同材質和相同形狀尺寸的鑄件,通過檢測線圈阻抗變化即可判定鑄件表面和近表面有無缺陷。
20世紀50年代初,德國福斯特Forster首創現代渦流檢測設備。我國渦流檢測技術的研究較晚,1963年上海材料研究所研制首臺渦流檢測儀。1993年愛德森(廈門)電子有限公司研制亞洲首臺全數字式渦流檢測儀。微電子學和計算機技術的發展,促進了多種渦流檢測技術的相繼出現,包括陣列渦流檢測、脈沖渦流檢測、遠場渦流檢測、三維電磁場成像等。
Giovanni Betta等提出一種采用線性調頻信號激勵渦流傳感器和探測信號譜分析的多頻渦流檢測方法,根據譜圖能量變化檢測鑄件缺陷,并對多頻渦流信號構建二維圖像,提升了缺陷識別能力。Saibo She等研究遠場渦流檢測技術優化問題,在探頭的激勵線圈與檢測線圈之間加入屏蔽板,使探頭尺寸大為縮小,同時在鐵磁管道外部引入一個鐵磁環以產生更大的磁通密度,進一步提高了檢測線圈的信號接收能力。
針對脈沖渦流探測中提振噪聲造成有用信息模糊的問題,Yating Yu等提出一種降低缺陷幾何信息提取噪聲的方法,有效降低了有色鑄件在脈沖渦流檢測中的噪聲,使缺陷定位更加準確]。Peng Li等提出一種選頻帶脈沖渦流檢測方法,與能量等價的方波脈沖渦流技術相比,對深度缺陷的響應更大更快。John R.Franzini 等設計了一種用于金屬鑄造的高分辨率熱成像檢測系統,可實時提供高清紅外圖像。B. Oswald-Tranta提出了主動脈沖紅外熱成像技術檢測方法,采用紅外熱像儀記錄金屬鑄件加熱和溫度降低過程,由于缺陷區比無缺陷區溫度更高,因此可以圖像的形式直觀顯示缺陷。
3.1.2 表面粗糙度檢測
鑄造表面粗糙度是指鑄造表面由具有較小間距的峰谷組成的微觀表面特性,是鑄件質量的重要參數之一,鑄造表面粗糙度的表征參數是縱向參數中的輪廓算數平均偏差Ra和微觀不平度十點高度Rz。鑄造表面粗糙度對交變載荷下鑄件疲勞強度和輸運管鑄件工作效率等影響極大。因此,準確評價并有效控制鑄造表面粗糙度具有重要意義。目前,鑄造表面粗糙度快速評價方法主要有標準樣塊比較法、觸針輪廓儀檢測法和計算機視覺評定法。
(1)標準樣塊比較法。標準樣塊比較法是一種快速測定鑄件表面粗糙度的簡便方法,比較樣塊不僅表面輪廓具有可比性,而且顏色也與鑄件表面顏色一致或相近,更加便于比對,檢測人員通過目測和觸摸對比確定被測鑄件表面粗糙度等級。根據國家標準制作的比較樣塊分為砂型、金屬型兩大基本類型,每種類型依據材質細分為鋼、鐵、銅、鋁、鎂、鋅等合金。
比較樣塊實物照片如圖21所示。
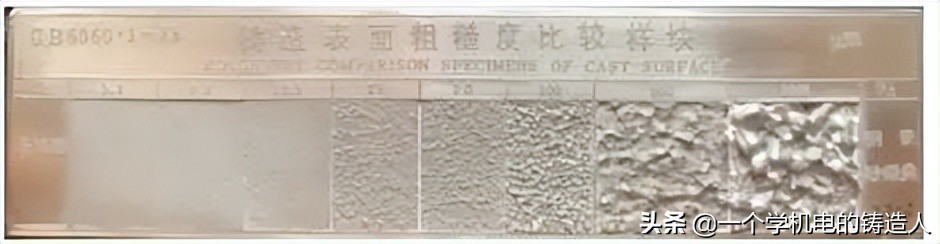
圖21 鑄造表面粗糙度標準樣塊
(GB/T 6060.1-1985)實物照片
(2)觸針輪廓儀檢測法。觸針輪廓儀法測定鑄造表面粗糙度,利用觸針式傳感器沿鑄件表面勻速滑動,記錄隨鑄件表面輪廓變化而產生的縱向位移和時間坐標,畫出觸針軌跡曲線并計算被測表面的Ra和Rz值。早期輪廓儀多采用電感式位移傳感器測定觸針縱向位移,后來改用半導體應變位移傳感器,檢測靈敏度更高。配套的數據采集與處理系統以PC和單片機為主。原哈爾濱科技大學是國內較早研制鑄造表面粗糙度觸針輪廓儀的單位,孟繁玉、王培東等開發了基于單板計算機的鑄造表面粗糙度測定儀,后期未見同類成果報道。目前,進口及國產的表面粗糙度測定儀器多為機加表面光潔度測定儀,鑄造表面粗糙度專用儀器尚不多見,有瑞士TESA Rugosurf 90G和日本產SJ-410便攜式機加表面光潔度測定儀。品類繁多的機加表面光潔度測定儀為新型鑄造表面粗糙度觸針輪廓儀研發提供了有益參考。
(3)計算機視覺評定法。計算機視覺技術的迅猛發展為鑄造表面粗糙度評定方法革新創造了條件,使以輪廓水平參數和高度參數對表面粗糙度進行三位評價成為可能,也推動了鑄造表面粗糙度三維評定標準制定工作的進步。
早期研究是采用平行光源以小角度照射被測表面,陰影部分寬度由入射角α和輪廓峰高決定。選陰影頻率f和陰影像素數D表征粗糙度。f表示測量長度內被測表面明暗交替的次數,代表輪廓的水平參數,與Sm(輪廓微觀不平度平均間距)和Sv(輪廓單峰平均間距)等參數相關;D表示陰影部分,在入射角α不變的情況下,與高度參數Ry(輪廓最大高度)和Rz(微觀不平度十點高度)等參數相關。入射角α對檢測結果影響很大,確定最佳入射角的方法是挑選兩個不同粗糙度等級的樣塊,采用不同入射角分別對兩樣塊進行測量,使兩者D值最大的入射角即為最佳入射角。
哈爾濱理工大學鑄造測控技術研究室嘗試以反映圖像紋理特征的直方圖均值和方差、單位表面頂點面積和峰谷陡峭度為特征參數評價鑄造表面粗糙度,證明特征參數與Ra和Rz有較好對應關系。
鑄造表面粗糙度三維評定標準亟需制定,鑄造表面粗糙度三維快速檢測儀器擁有較大發展空間,特別是基于計算機圖像識別的鑄造表面粗糙度便攜式檢測裝置將更受歡迎。
3.2 鑄件內在質量檢測
鑄件內在質量包括內部缺陷和內在組織兩大方面。典型內部缺陷主要有裂紋、氣孔、縮孔(松)、夾雜等,這里所說的內在組織主要指特殊析出相和基體組織。針對鑄件典型內部缺陷和組織的無損檢測方法主要有射線、超聲、紅外、電磁(阻)和音頻等檢測方法。
3.2.1 內部缺陷檢測
(1)射線法檢測鑄件缺陷。采用X射線、γ射線和中子射線作為射線源,基于不同材料對射線衰減程度不同的原理,鑄件內部缺陷引起透射射線強度發生變化,通過檢測射線強度即可判斷缺陷的位置、大小和性質。
射線檢測技術分為照相檢測、實時成像檢測、層析檢測和其他射線檢測技術。射線照相檢測是最傳統的無損檢測技術之一,因具有影像直觀、查看方便等特點,曾被廣泛用于鑄件裂紋、孔洞、夾雜等缺陷檢測。實時成像檢測技術通過圖像增強設備在顯示器上形成相關信息的圖像,利用計算機和數字圖像處理技術,將缺陷成像直接呈現在顯示器上,檢測效率更高,更便于實時分析。射線層析檢測是能夠實現三維成像的檢測技術,通過工件材料、結構、組成及密度等特性獲得相應的二維斷層圖像,根據數據對圖像進行重建獲得三維圖像。
在二維成像方面,Wenquan Lu等采用基于同步加速器的放射成像技術對鑄造過程中的鑄件表面進行高效成像,用于實時調整冷卻速率以避免偏析產生。
Wang Kang-yi等設計了一種基于CCD的數字射線探測系統,能接能量范圍更廣的X射線,從而獲得成像質量更高的檢測結果。Cheng Jin等提出一種基于Relief算法和Adaboost支持向量機的內部裂紋檢測方法,具有比現有常用分類器更高精度及泛化能力,圖像處理算法應用前景可觀。
在三維成像方面,Anton du Plessis等利用X射線微計算機斷層掃描技術構造鈦合金航空鑄件內部的清晰視圖, 根據孔洞類缺陷的體積形態對其進行著色分類,圖22a-b分別為鑄件CT斷層掃描和壁厚分析三維圖像。Zhuofei Yang等采用X射線計算機斷層掃描(CT)技術, 精確測量氣孔類缺陷和疲勞裂紋,圖23為拉伸試棒和航空件的原圖像(a)及CT圖像數據(b),孔洞類缺陷部位呈顆粒狀。Changhui Liu等研究了環形鑄件尺寸測量方法,將極坐標引入確定性定位偏差分析的算法中,用CT重構鑄件外觀尺寸及壁厚,使計算過程更為簡單。Steven Oeckl等研究X射線計算機斷層掃描重建和圖像處理相結合處理技術,對汽車鋁鑄件中潛在缺陷區進行高分辨率層析成像,對其他區域采用低分辨率重構,可在短時間內完成全鑄件缺陷檢測。
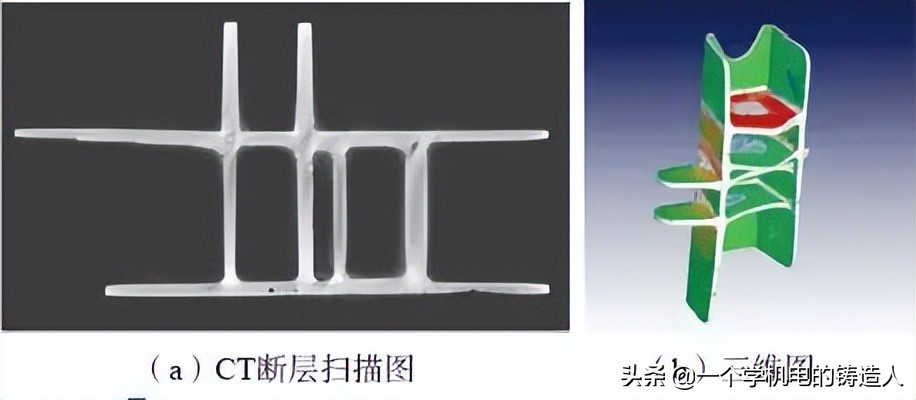
圖22 鑄件CT斷層掃描圖像及壁厚分析三維圖
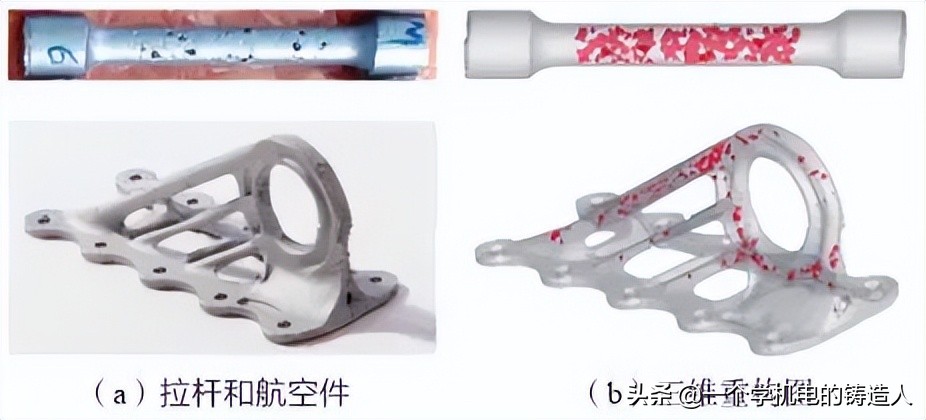
圖23 鈦合金拉伸桿和航空件原圖及三維重構圖
德國Andreas Beyer設計了一種可滿足多種形狀、尺寸大到1200mm×1800mm的鑄件進行批量X射線檢測工藝,最終由Yxlon公司推出系列產品。X射線檢測單元的核心部分包括:用于檢測單元長期、穩定、安全操作的防輻射柜;用于快速生成必須檢測位置的多軸定位系統;實現檢測結果再現的成像系統,包括X射線源、X射線探頭以及模擬或數字圖像增強裝置;符合人體工程學的控制系統。近年來,國內X射線探測設備專業生產廠及鑄造企業在新技術開發及應用方面也取得可喜進展。中國一拖集團有限公司賈天儀等自主研發X射線實時檢測系統,包括X射線、實時成像、機械傳動、電氣控制、射線防護等單元,系統檢測結果與鑄件解剖試驗結果相符。多家射線探測專業生產企業運用DR成像技術呈現三維圖像檢測結果,如丹東奧龍射線儀器集團有限公司生產的高能工業三維立體成像設備和日聯科技生產的UNC系列X射線成像檢測系統。
X射線檢測技術正朝全尺寸、高精度和高時效方向發展,這一點已為國內外研究成果及產品特點所證實。
(2)超聲波檢測鑄件缺陷。超聲波檢測是國內外應用最廣泛、使用效率最高、發展最快的無損檢測方法。超聲波在材料中能以一定速度和方向傳播,遇到聲阻抗不同的異質界面(如缺陷或被測工件的底面等)就會產生反射、折射和波形轉換,根據接收到的超聲波特征信號可判斷是否有缺陷存在。早期的鑄件缺陷常規超聲檢測技術主要基于脈沖反射法和穿透法,根據發射波、缺陷波和底波相對于掃描基線的位置確定缺陷位置,根據缺陷波幅度確定缺陷大小,根據缺陷波形狀分析缺陷性質。常規方法雖然能對缺陷進行定位和定量檢測,但檢測結果只是一維圖像且存在一定檢測盲區,不能實現鑄件的全身體檢。
隨著計算機技術的快速發展,超聲成像檢測應運而生,包括時間反轉法、掃描成像法、超聲相控陣法等新技術在多種材料缺陷檢測中得到廣泛應用。
H u i f a n g X i a o 等結合改進的超聲測量模型(IUMM)和支持向量機(SVM),提出一種使用掃描聲顯微技術識別金屬材料中夾雜和空洞的新方法,試驗證明IUMM預測的回波信號在幅度和頻率上比傳統的UMM更為準確,SVM分類器能成功區分夾雜和孔類缺陷。蘇宣機等運用相控陣超聲波技術探測正火狀態下的閥門鑄鋼試件,可快速獲得C、B、D、S掃描和A型脈沖顯示及三維立體成像,缺陷表征與實際缺陷存在偏差,適當提高增益可提高缺陷分辨率,從而增加缺陷類別的可靠性。蔣毓良等將超聲相控陣技術用于輪轂球鐵件缺陷檢測,證明檢測外形復雜、壁厚較大的鑄件時,低頻探頭與高頻探頭、標準楔塊與特制楔塊、扇掃探頭與線掃探頭聯合使用;超聲相控陣能分辨出相鄰較近的小缺陷,能更準確地測量缺陷密集區的厚度方向尺寸。Wolfram A.Karl DEUTSCH等研究全聚焦相控陣超聲檢測技術(TFM),對表面紋理呈樹枝狀的鋼和輕合金鑄件進行全聚焦高分辨成像試驗,由于TFM可從不同方向傳輸和接收超聲信號,可覆蓋大范圍探測區域,缺陷尺寸檢測精度有大幅提高,鑄鋼件缺陷探測及高分辨成像見圖24。朱學耕等利用相控陣超聲檢測儀檢測葉輪與齒輪內人工預置平底孔缺陷,得到清晰的缺陷信號,利用缺陷信號分析缺陷位置,對葉輪盤及齒輪輪齒內缺陷定位誤差僅為0.9%和0.28%,證明相控陣超聲檢測鑄件缺陷具有較高定位精度。
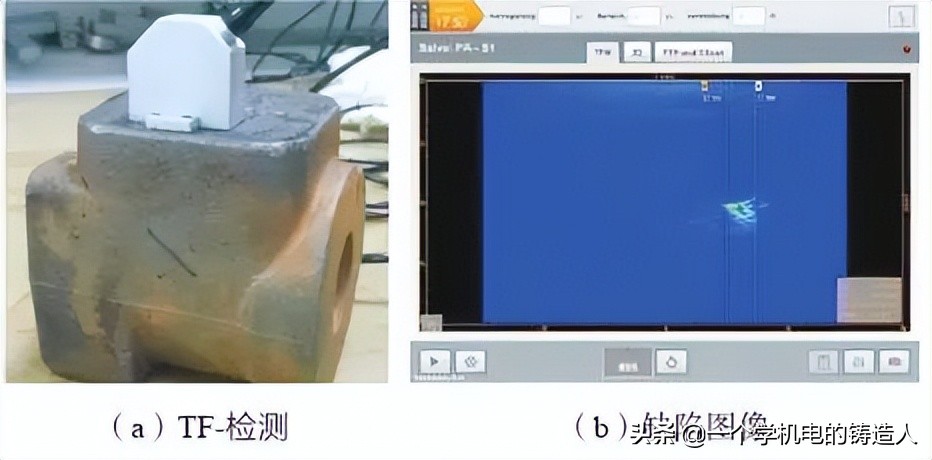
圖24 鑄鋼件TFM檢測及高分辨成像
另一種非接觸高精度超聲檢測新技術——激光超聲檢測技術值得關注,采用激光脈沖照射工件,工件表面吸收來自激光的能量迅速升溫,通過熱彈效應或熱蝕效應在表面產生應變、應力場,使粒子產生波動,進而誘導工件內部產生超聲波。隨后用光學法接收超聲信號,從而獲取工件厚度、內部及表面缺陷等參數。與空氣耦合超聲、電磁超聲、靜電耦合超聲檢測相比,激光超聲檢測具有顯著優勢。Peipei Liu等采用基于雙激光超聲系統的雙激光誘導非線性超聲調制技術,檢測金屬鑄件樣品中的疲勞裂紋,獲得滿意效果。Yong-qiang Liu等提出一種基于非線性激光超聲和狀態空間的方法,采用兩個激光脈沖掃描后鑄件產生超聲波,由高頻傳感器記錄波形數據,然后重建基于狀態空間的吸引子,再通過觀察平均局部吸引子方差比的空間分布,實現鑄件裂紋的高效檢測。
Hubert Grin等和Jürgen ROITHER等采用激光超聲設備對連續鑄造的鋁板進行在線超聲檢測,其超聲信號幅度及頻率與微觀結構噪聲的變化規律均證明激光超聲檢測凝固裂紋缺陷可行。
日本Olympus公司推出一種能夠實現動態聚焦的OmniScan X3相控陣超聲成像探傷儀,設備同時搭載了聲學影像工具和掃查工具,可同時顯示4種模式不同角度的圖像。我國廣東汕頭超聲電子股份有限公司自主研發的CTS-PA322T相控陣超聲檢測儀,可用于復合材料、不銹鋼、殼體鑄件、復雜鍛件等工件的高精度全聚焦實時超聲成像檢測。
2008年,日本筑波科技株式會社首次研制了LUVI激光超聲波可視化檢測儀。利用激光脈沖照射被測物體表面產生超聲波信號,可實現超聲波實際傳播過程的動態觀測,具有豐富的圖像處理和信號處理功能。PAR system LLC公司的LaserUT Premium Gantry激光超聲無損檢測系統,可在無需鑄件移動的情況下檢測任何部位,特別適合重大型鑄件檢測。
(3)紅外及紅外熱波法檢測鑄件缺陷。紅外檢測的基本原理是基于物體熱輻射特性,由于缺陷和材料熱特性不同表現出溫度差異,通過掃描記錄或觀察試件表面溫度變化而發現缺陷的存在。基于紅外檢測原理的檢測裝置主要有紅外熱像儀、紅外熱電視、紅外測溫儀和紅外照相機等。我國1968年開始紅外檢測技術研究工作,紅外探傷儀于1981年后廣泛用于金屬材料、復合材料近表缺陷檢測。
紅外熱波法是一門跨學科技術,其特點是適用面廣、速度快、觀測面積大、定量、直觀。紅外熱波理論研究的熱點是熱源,特別是變化性熱源與媒介材料及其幾何結構之間的相互作用。通過控制熱源激勵方法與測量材料表面溫場變化,獲取材料表面及以下的結構信息。紅外熱波檢測的核心是針對被檢物材質、結構和缺陷類型設計不同熱源并采用計算機控制脈沖式加熱,同時采用紅外熱成像技術對時序熱波信號進行數據采集,采用專用軟件進行實時圖像信號處理并顯示檢測結果。
南京工業大學陳曦等研究基于紅外熱成像的金屬材料氣孔缺陷識別技術,采用5 000 W鹵素燈照射被測件,利用FLIRSC660紅外熱像儀拍攝表面紅外熱圖像,通過Open CV 軟件完成高斯低通濾波、紅外缺陷熱圖像直方圖均衡化、圖像閾值化和邊緣檢測。德國G.Walle等研究低頻電磁感應加熱鐵磁性鋼件缺陷熱成像技術,通過對內部電流和溫度分布的數值模擬和對人造與自然裂紋的實測試驗,發現板件有背面起裂隱藏裂紋時,其缺陷與電磁感應頻率的關系反常。韓國Wontae等研究了材料次表面缺陷紅外熱波探測熱成像技術,成像方法可廣泛用于工業領域金屬材料缺陷檢測中的紅外熱成像,試驗結果證明,采用MATLAB成像是較好的選擇之一。加拿大Davood Kalhor等研究地下鋼管表面空洞紅外熱成像探測方法,采用長脈沖熱像圖譜,結合前后處理算法實現識別,證明空洞尺寸及位置信息均可從熱像圖譜中提取。南京工大杜雪雪等設計了一種主動式紅外熱像金屬板缺陷NDT檢測系統,針對原始紅外圖像存在裂紋缺陷輪廓模糊、環境噪聲干擾等問題,提出采用圖像灰度轉換、直方圖均衡化、中值濾波、閾值分割和邊緣檢測等方法提取裂紋缺陷邊緣輪廓特征。中北大學研究基于激光熱成像的金屬表面檢測技術,搭建了一套基于透射式激光熱成像檢測系統,使用COMSOL軟件仿真驗證方法有效性,結合試驗對金屬表面不同深度的微小裂紋進行量化分析,實現了表面缺陷的三維表征。
由其檢測原理決定,紅外及紅外熱波成像缺陷檢測技術,用于鑄件缺陷在線檢測具有獨特優勢。是否可以利用鑄件冷卻過程中缺陷部位與非缺陷部位降溫速度差異,直接抓取鑄件表面紅外熱像,通過去偽、濾噪等處理,提取缺陷信息,相關問題值得開展試驗研究。
3.2.2 內部組織檢測
鑄件內部組織無損評價是鑄造工作者一直關注的課題,基于對鑄件不同內部組織與能量場之間相互作用的深入研究,使超聲波、音頻振動、電學及磁學等無損檢測手段用于鑄件金相組織及力學性能評價成為現實。
(1)超聲波檢測鑄件組織性能。由于超聲波在不同介質傳播時與微觀組織的相互作用,通過對傳播速度、衰減、背散射振幅、光譜和臨界角等超聲參數分析,可以獲得材料微觀組織信息,這是超聲波檢測鑄件組織性能的基本原理。目前,超聲波主要用于檢測鑄鐵件石墨形態、鋼鐵件基體組織及力學性能。
超聲聲速檢測鑄鐵石墨形態基于公式(3)。
Cl=[E(1-σ)/ρ(1+σ)(1-2σ)]1/2 (3)
式中:Cl為超聲縱波速度;E為介質楊氏彈性模量;σ為泊松比;ρ為介質密度。E與被測材料球化級別直接相關。
英國R.J.M. Stokes等在20世紀80年代初期發表論文顯示,球墨鑄鐵中碳飽和程度和鑄造時澆注速度直接影響超聲波速度和衰減程度,飽和程度越高,超聲速度越低、衰減程度越大。論文給出了三種判定球鐵球化率的方法,即超聲速度法、標準厚度衰減法和標準厚度速度法。W.Orlowicz等通過試驗總結出超聲波速CL與石墨形狀系數SS和單位面積石墨析出個數NA(mm-2)之間關系式,以及石墨形狀系數SS、單位面積石墨析出個數NA和縱波聲速CL與抗拉強度UTS(MPa)的關系式:CL=3218.4SS+5407.6(R=0.99),CL=0.188 7NA+5567.6(R=0.99);UTS=4446.9SS+207.63(R=0.99),UTS=0.608 4NA+406.23(R=0.99),UTS=1.263 1CL+663 1.7(R=0.99)。Freitas等通過對不同基體組織AISI鋼的超聲速度測量,波速由高到低依次為鐵素體、珠光體和馬氏體,馬氏體超聲聲速低的原因是大量四邊形晶格扭曲,增加了晶粒彈性各向異性所致,而珠光體超聲傳播速度低于鐵素體的原因是滲碳體的影響。Toozandehjani等研究了熱處理過程中微觀組織演變的超聲特征,利用超聲檢測技術檢測了各種材料相變、析出和時效硬化反應。
天津大學郭亞飛20世紀90年代后期研究發現,石墨形狀與超聲波速度有明顯對應關系,但基體組織與超聲波速之間并無顯著關聯。鐵素體、珠光體、正火馬氏體和貝氏體有相同特性,較大數量正火馬氏體和珠光體會導致超聲幅值增大。Kenaway M.等研究利用超聲技術檢測球墨鑄鐵缺陷和冶金性能,建立了超聲聲速與球化率和碳當量之間的關系。KenawayM.還研究了采用脈沖反射法測定超聲速度和衰減,進而測定球墨鑄鐵硬度、脆性、抗拉強度等力學性能和珠光體、鐵素體等級等。Toozandehjani M.等研究材料微觀組織和超聲特性,認為超聲技術可用于多種材料力學性能及微觀組織轉變評價。Khan S.研究用超聲無損評價SISI316L不銹鋼材料性能,結論是超聲參數與材料力學性能密切相關。國內許多高校和企業結合生產需要開展了不同形狀鑄件的球(蠕)化質量超聲檢測技術研究。廖智等開發了由超聲波發射電路、接收電路和厚度偏差補償電路構成的球墨鑄鐵球化率超聲檢測系統,測得與1-6級球化對應的超聲波速度。
李世強等采用超聲波橫波聲速表征離心球鐵管球化率,證明橫波聲速隨球化率增大而增大,原因是聲速取決于材料彈性模量、泊松比和密度等受石墨形狀影響顯著的特性參數。張文杰等先后研究了球墨鑄鐵件和蠕鐵制動轂蠕化率超聲檢測技術,并分別給出了聲速值與球化率和蠕化率的關系式,聲速值=6.556×球化率+5058.8;聲速值=-8.715×蠕化率+5949.2。
(2)音頻振動檢測鑄件組織性能。民間用敲擊瓷器產生的余音高低識別其質量優劣,鐵路機修工人靠錘頭敲振機車零部件發出的聲音粗細判斷是否潛藏故障,兩者都是音頻檢測方法的應用。現代音頻檢測方法是利用音頻共振方法對被測件施振,通過測定被測件共振頻率評價內部組織異同。一階共振頻率f與材料楊氏模量E的平方根、鑄件密度ρ和形狀因素υ成正比,對于某一定型產品而言,密度和形狀因素可視為不變,則共振頻率f與楊氏模量的關系可寫成式(4)的形式。
f = k E1/2 (4)
式中:k為與鑄件密度、形狀等相關的常數。楊氏模量E受化學成分、基體組織、工藝條件等影響,其中石墨形態影響最大。
音頻檢測的另一個重要參數是內耗值。內耗是由于材料內部的原因使機械能損耗的現象,實際應用中常用振動系統的品質因數Q的倒數作為內耗的度量,即:
Q-1=δ / π (5)
式中:δ為振動對數衰減率,可通過n次振動前后兩次振幅比值的對數除以n獲得。
第二汽車廠徐光清等于氣管固有頻率偏高,由此確定510~580Hz范圍為蠕化率合格排氣管。90年代中期,賈健生等研究振動法檢測球鐵曲軸球化質量,采用機械激振器施振,拾音器采集曲軸振動信號并分析,獲得固有頻率與球化率之間的關系。柏逢明采用Φ10mm×100mm鐵素體球鐵試棒和Φ10mm×150 mm珠光體球鐵試棒檢測分析,分別獲得球化率與共振頻率的關系和鐵素體及珠光體含量與內耗值的關系,在此基礎上,與吉林工大和一汽集團合作研制了球墨鑄鐵軸類件用音頻檢測儀。曾輝等研究音頻法檢測鑄件球化級別,采用Φ30 mm試棒測試不同球化級別試棒的共振頻率,1、2級球化固有頻率為600Hz以上,5、6級球化固有頻率為400Hz以下。周飛采用音頻檢測蠕鐵飛輪固有頻率,確定了被檢鑄件蠕化率與固有頻率的對應關系。為了消除鑄件尺寸變化對共振頻率預測鑄鐵球化和蠕化率的影響,徐從裕等提出由多個共振頻率組成的多模態音頻檢測模型,模型系數由音頻檢測數據通過在線學習獲得。試驗結果證明,多模態音頻檢測模型能有效識別鑄件彈性模量變化及變化規律,而與鑄件尺寸無關。
(3)電磁方法檢測鑄件組織性能。電磁無損探傷具有悠久的研究及應用歷史,用于鑄件組織性能的電磁檢測方法主要有巴克豪森噪聲檢測、渦流檢測及電磁超聲檢測等。
巴克豪森噪聲于1919年由德國物理學家Barkhausen發現,將一導體線圈置于材料表面并對材料施加交變磁化場,材料磁疇的不可逆轉跳躍將在線圈內感應一系列電壓脈沖信號,通過擴音器放大后可聽到沙沙的噪聲。磁疇壁的不可逆運動除產生噪聲外,還能激發一種稱為磁聲發射(MAE)的彈性波,可通過壓電晶體傳感器加以接收。
巴克豪森噪聲可用于檢測材料晶粒度熱處理狀態、硬度等各種力學性能。低碳鐵素體鋼和鐵素體-珠光體鋼都可用巴克豪森噪聲法測定晶粒度;巴克豪森法對時效、珠光體形貌及碳含量也很敏感;巴克豪森噪聲與高合金鋼在淬火、回火和塑性變形時的關系已很清楚,采用巴克豪森噪聲檢測不銹鋼熱處理前后微觀組織結構變化以達到實用階段。
李強等人和李志譚等人在同一時期利用巴克豪森效應檢測了鐵磁性材料的晶粒度,均提出利用波形半高寬占空比作測量參數表征晶粒大小。Anglada-Rivera J等研究外加應力及晶粒尺寸對Bakhaosen噪聲和磁滯回線的影響,發現B噪聲效應幅值隨外加應力增加到最大值后開始減小,細晶粒的B效應幅值遠大于粗晶粒B效應幅值。Yamaura S等研究晶粒尺寸對純鐵試樣B噪聲的影響,證實B噪聲與依賴晶粒尺寸的Hall-__Petch關系具有相關性。Ng D H L等研究含α鐵和滲碳體的碳素鋼中碳含量與B噪聲參數的關系,證明B噪聲信號中半值寬度幅值、噪聲信號曲線下面積與碳含量相關。Normando P G等用超聲和渦流技術對雙相不銹鋼σ相檢測,證明阻抗和超聲聲速對σ相敏感。
潘立等采用不同回火溫度處理獲得不同硬度的45號鋼,試驗發現隨回火溫度升高和材料硬度漸小,巴克豪森信號特征值隨之升高,其中振鈴計數對硬度變化反應最為敏感。夏鵬等采用巴克豪森噪聲、增量磁導率和切向磁場強度等多項電磁特征參數,通過挑選R2值較大的參數作輸入樣本,采用人工神經網絡建模方法,對鐵路車輪鋼表面硬度定量測量,獲得滿意效果。
李云飛等認為,常規渦流只與磁化曲線中的線性部分相關,即視材料相對磁導率為一常數,如果激勵磁場信號放大,受鐵磁材料磁導率影響,B-H磁化曲線將進入非線性部分,并在導體材料感生出非線性渦流,此時即使輸入單個頻率的交流激勵信號,檢出信號也會產生多個頻率的諧波響應,而頻譜分析后的幅值及B-H非線性曲線與材料塑性變形損傷存在關聯性,對304奧氏體不銹鋼和Q195碳素鋼檢測證明,損傷程度與檢測信號頻譜圖的基頻幅值、三次諧波幅值存在一定線性關系。任尚坤等研制搭建了一種靈敏微分磁導率檢測實驗平臺,采用測量低場磁化曲線的方法對碳素鋼材料靈敏微分磁導率進行了驗證測量,理論證明了檢測信號與微分磁導率成正比,試驗發現20鋼、35鋼和235鋼的靈敏微分磁導率即初始微分磁導率與振動平臺磁強度計低場磁化曲線測量結果一致,靈敏微分磁導率隨拉應力的變化率足夠明顯。王蓉等檢測了不同鐵素體含量球墨鑄鐵樣件的磁性,結果表明,在低磁場下,磁化強度與試樣鐵素體含量沒有關聯性,但當磁化強度增大到球墨鑄鐵件趨于磁化飽和階段時,磁化強度與鐵素體含量相關,在相同勵磁電流作用下,磁化強度隨鐵素體含量增加而增大。
趙軍輝等研究電磁超聲檢測各向同性金屬材料彈性模量,采用大功率超聲檢測儀激發電磁換能器獲得超聲橫波、縱波和模式轉換的橫波和縱波,檢測20鋼CSK-IIA標準試樣,通過分析波包最大幅值和時間,達到快速準確檢測楊氏模量和泊松比的目的。趙素貞等研究金屬材料缺陷的電磁超聲/渦流復合檢測技術,設計了同時滿足電磁超聲和渦流檢測的復合探頭,仿真和實驗結果表明,復合探頭不僅可以快速檢測表面裂紋,而且可以激發具有明顯指向性的縱波,一定程度上削弱了波形轉換產生的干擾波,有利于內部缺陷的準確識別和定位。饒臻浩等提出一種集成漏磁、電磁超聲和導波電磁檢測軟件的可復用結構設計方法。采用模塊化模型思路設計功能模塊,基于軟件總線結構概念實現模塊間數據通信,通過設計標準化數據接口,以滿足各模塊的獨立開發和拓展,并與軟件系統無縫連接,使用調度控制器進行檢測模式或狀態的切換,從而實現多種檢測功能。
4 鑄造生產在線檢測技術發展趨勢分析
智能鑄造、綠色鑄造對鑄造在線檢測技術提出了越來越高的要求,以更多角度、更快速度和更高精度完成參數檢測,服務于合金熔煉、配砂造型和鑄件分揀三單元閉環控制系統形成和基于三閉環的智能鑄造車間構建,是鑄造在線檢測技術的努力方向和發展目標。
4.1 合金熔體質量在線檢測
合金熔體的合格標準是溫度、化學成分和純凈度滿足設計要求,在貫徹熔體管理理念的前提下,還需要在溫度協同管理、爐前成分分析、純凈度監測和組織性能快速預測方面研究應用新技術。
(1)熔體溫度協同管理技術。熔煉溫度、出爐溫度、爐前處理溫度、出包溫度和澆注溫度需要協同管理、精準設定和檢測,并根據設定和實測結果實時優化調整。目前,國內大部分鑄造車間在熔體溫度協同管控方面仍有較大差距,定溫不科學和測溫不及時的情況不同程度存在,爐前多點位測溫及智能控溫系統將有需求。
(2)熔體化學成分原位分析方法及裝置。目前,雖然已有爐前取樣直讀光譜化學成分分析和基于LIBS原理的熔體化學成分原位分析,但現有技術和裝備還不能完全滿足各類合金及不同規模鑄造車間的多樣化檢測需求。熔體化學成分原位分析新方法及多手段組合的快速分析系統有待研究和應用。
(3)熔體純凈度快速評價方法及裝置。熔體純凈度主要包括含氣和夾雜程度,目前測氣測雜技術在檢測速度和檢測精度方面均有較大提升空間。系統深入研究各類合金熔體氣、雜形成機制,開發基于濃差電池等原理的在線測氫裝置和基于超聲及其他非接觸檢測原理的熔體夾雜含量快速檢測裝置應為當前工作重點。
(4)熔體結晶組織性能爐前預測方法及裝置。熔體結晶組織性能預測是生產高品質鑄件的重要監控手段,諸如熱分析、熱物性檢測的預測方法仍然具有較強的生命力。目前對熱分析取樣器和冷卻曲線特征參數研究的系統性還需進一步加強,包括試樣凝固過程熱交換條件保證及人工智能在數學建模中的應用等。同時,熔體電導率、熱導率、粘度、表面張力等熱物性參數在凝固過程中的變化用于預測結晶組織及性能具有極大潛力,有必要開展系統的基礎研究和系列檢測新技術開發。
(5)熔體冶金質量智能診斷專家系統。綜合熔體溫度、化學成分、純凈度監測及結晶組織性能預測結果,實時分析當前熔體冶金質量、存在問題、給出最優解決方案并驅動執行機構執行,是合金熔煉閉環控制系統的控制路徑。其核心部分是冶金質量智能診斷專家系統,要在前述四類參數檢測和預測的基礎上融合學科知識、專家經驗、車間歷史等模塊通過演繹推理做出科學判斷。鑄造專家系統雖有研究應用,但針對熔體冶金質量優化控制的專家系統,還需要針對新要求認真構建。
4.2 濕型砂及砂型質量在線檢測
鑒于濕型粘土砂鑄造仍為當前主要鑄造成形方法,本文未涉及樹脂砂鑄造、殼型鑄造及3D打印砂型等其他金屬成形方法的配砂及造型中的檢測技術。為了適應不同鑄造車間配砂系統控制策略及造型線質量控制原則的實際需要,濕型砂質量在線檢測技術主要向性能為主和組分為主檢測的兩個方向發展,砂型在線檢測技術則聚焦表面粗糙、強度和型芯組合精度檢測。
(1)濕型砂性能評價方法及裝置。基于型砂性能的配砂控制系統,主要關注型砂的濕強度(包括濕壓、濕拉、剪切或劈裂等)指標。從濕型砂質量在線檢測技術發展軌跡可見,國內外性能檢測參數在向少而精的方向發展,緊實率和濕強度為必檢或首檢參數,其他諸如透氣性、型砂組分等不予檢測或僅作參考。基于這一原則,以型砂強度和緊實率為主要檢測參數的固定在線自動檢測裝置、車間移動式自動檢測裝置和便攜式微型檢測裝置均是今后一個時期的需求重點。
(2)型砂組分快速檢測方法及裝置。從理論上講,在配砂工藝和生產任務比較穩定的鑄造車間,只要循環砂主要組分能得到有效控制,其性能就可以保證穩定。因此,可以構建從組分檢測到組分控制的直接優化控制系統。直接優化控制系統需要在線精準測定回用舊砂及混砂機出砂溫度、含水量、有效粘土含量,含水量檢測和有效粘土含量檢測,需要在現有間接檢測方法基礎上,繼續探索和開發更快、更準的檢測新方法及在線、移動和便攜式檢測裝置。
(3)砂型質量跟蹤監測系統。砂型質量全面跟蹤監測對于生產高品質鑄件至關重要,監測內容不僅包括砂型表面光潔度及強度,還包括芯、型組合尺寸精度等。目前砂型質量監測內容有待進一步豐富或改進,為此需要研究開發高精度砂型表面光(清)潔度、芯、型組合尺寸偏差及砂型表面強度跟蹤監測系統,該系統具備廢品智能識別和(砂)型、(鑄)件綁定功能。
(4)型砂及砂型質量智能診斷專家系統。鑄件缺陷約60%以上源于型砂質量,DISA公司采用數字化工具設計了一種型砂質量智能管理系統-Monitizer CIM,采集數據包括與型砂質量關聯度較高的配砂、造型、熔煉及落砂工位14個參數,信息參數自動采集并通過云平臺技術管理和應用。國內鑄造車間尚無如此全面的實用化型砂管理專家系統,在進一步完善和創新在線檢測技術的同時,盡快開發適合國情的型砂及鑄型質量智能診斷專家系統,對于加快智能鑄造車間建設具有重要意義。
4.3 鑄件質量在線無損檢測
我國無損檢測技術研究應用起步較晚,與其他行業相比,鑄件無損檢測技術水平還有明顯差距。目前,國內配備鑄件內、外質量全方位在線無損檢測的鑄造生產線還很少,且多數鑄造車間在鑄件在線無損分揀方面尚屬空白,鑄件缺陷只能靠人工目測進行簡單識別,技術進步任重道遠。
(1)鑄件表面質量在線檢測。針對表面裂紋、穿透裂紋、夾砂、鼠尾、澆不足等表面可見缺陷,采用基于紅外熱像原理的在線檢測系統配套機器人視覺完成缺陷線上識別,重要鑄件或鑄件重要部位進行線下磁粉檢驗和渦流探傷,應該是鑄件表面質量檢測較為現實的中期目標。鑄造表面粗糙度檢測當前亟待開發便攜式表面粗糙度檢測儀,同時需加快制定鑄造表面粗糙度三維評價標準和研制基于計算機視覺的三維表面粗糙度測定儀。
(2)鑄件內部缺陷在線檢測。重點研究開發適合不同形狀、尺寸及合金材質的X射線無損檢測裝備、紅外熱波探測裝備及激光(電磁)超聲等非接觸無損檢測裝備。鑒于射線和超聲對被檢鑄件的特殊要求,可設計獨立成線且具有自動上料、自動上臺和自動卸料功能的鑄件無損探測平臺。
(3)鑄件組織性能無損評價。鑄件組織性能無損評價并非鑄造生產流程必備檢測環節,但在智能鑄造框架下卻具有非常重要的實用價值。無需破損檢驗即可獲得鑄件組織性能參數與鑄件生產同步采集的合金熔體、配砂造型、澆注凝固等眾多參數構成的每個鑄件獨有的大數據,通過系統大數據分析,實現鑄件生產工藝的不斷優化,最終獲得鑄件品質的極致提升。鑄件組織性能無損評價技術發展的重點是基于超聲、音頻和電磁檢測原理,具有鑄件標識讀取功能的鑄件晶粒度、鑄鐵石墨形態及硬度和強度評測裝置。
5 結束語
本文以順應智能鑄造和綠色鑄造發展趨勢,發掘鑄造快速檢測技術發展空間和潛力為出發點,概述了鑄造生產過程合金熔煉、配砂造型、鑄件質量在線快速檢測技術研究及應用進展情況,簡要分析了三類快速檢測技術發展方向。
(1)經過改革開放以來40余年的發展,我國鑄造生產快速檢測技術研究及應用取得了長足進步,在鑄造大國的鑄造生產中發揮了重要作用。
(2)鑄造在線檢測技術總體水平與工業先進國家相比仍有較大差距,研究層面創新不足,應用層面不平衡和不充分問題比較突出。
(3)在大力發展智能鑄造和綠色鑄造的背景下,在線快速檢測技術發展空間巨大,熔體質量爐前檢測、配砂造型在線檢測和鑄件質量無損檢測均有較大潛力可挖。
注明:本文章來源于互聯網,如侵權請聯系客服刪除!